Catalog
This article presents an application approach of using a MEMS absolute pressure sensor in wearable devices to measure both altitude and diving depth simultaneously. Using the WF282A sensor as an example, it is very small, highly accurate, and low-power (wfsensors.com). The article analyzes the different requirements and challenges of altitude vs. underwater measurement, explains the WF282A’s key technical parameters and advantages, including high accuracy, ການບໍລິໂພກພະລັງງານຕ່ໍາ, packaging and interface design, ແລະອື່ນໆ. It also discusses key points for soldering and mounting the sensor in the device, the testing procedures and instrument selection before mass production, and the mode-switching algorithms with environmental compensation between altitude and diving modes. Targeted at developers of wearable sports devices, this article is concise and reader-friendly, helping readers understand and apply multi-functional absolute pressure sensor technology.
Dual Application Challenges of MEMS Absolute Pressure Sensors in Altitude and Diving Measurements
Altitude Measurement Environment
In the air, measuring altitude is mainly based on atmospheric pressure changes. As altitude increases, pressure drops about 1 hPa per 8 meters, meaning a centimeter of height change corresponds to only about 0.01 hPa. ເພາະສະນັ້ນ, altitude measurement requires a sensor with very high resolution and temperature stability. In practice, devices often calibrate the reference pressure at startup or at a known elevation (using GPS or reference data) to improve accuracy. Atmospheric temperature and weather conditions cause pressure fluctuations, so the sensor must compensate for temperature and humidity changes. The air is dry, but sudden weather changes (like the onset of a storm) can disturb readings. To handle rapid vertical movements (such as climbing stairs), you also need sufficient sampling rate and filtering to capture the dynamic altitude changes.
Underwater Measurement Environment
Underwater, the sensor is subjected to much higher pressure than in air. According to NOAA, pressure increases by about one atmosphere for every 10 meters of water depth. Thus when diving, an absolute pressure sensor reading includes both the pressure from the water depth and the surface atmospheric pressure. The sensor must be sealed and waterproof, and its measurement range must cover the desired depth. You can record a reference pressure P0 at the surface before diving, and use that as the baseline to compute depth during the dive. Additionally, water temperature and salinity changes affect water density and thus the depth calculation; these can be corrected with compensation factors. Over long dives, sensor drift can also introduce errors, so periodic recalibration or algorithmic correction is needed.
Measurement Range and Accuracy Requirements
In altitude mode, pressure changes are very small. For example, a 3-meter height difference between floors corresponds to only about 30 Pa. The WF282A in high-precision mode can provide ±0.006 hPa (about 5 cm) resolution, meeting stringent altitude measurement needs. Diving depth measurements require a much wider pressure range: every 10 meters of freshwater adds about 1000 hPa. Note that the WF282A’s range is 300–1200 hPa (about 1100 m altitude or 10 m water), so it cannot measure beyond this range. Temperature changes also affect the sensor output and must be compensated.
Mode Switching and System Design Challenges
A dual-mode application requires the device to switch between altitude and diving modes. This means the system must detect if it is underwater (e.g. by a rapid pressure rise beyond the normal atmospheric range) and choose the appropriate calculation. A simple strategy is to switch to dive mode when the pressure exceeds a threshold (say 1100 hPa) for a sustained period, to avoid false triggers. In altitude mode the standard atmospheric formula converts pressure to height, whereas in diving mode the hydrostatic formula is used to compute depth. The baseline atmospheric pressure and calibration differ between modes, so the system design must consider how to store and update environment parameters (such as the surface pressure P0) to ensure seamless switching. An optional manual mode switch can also be provided as a backup.
Key Technical Advantages and Specifications of the WF282A Sensor
High Accuracy Performance
The WF282A sensor delivers extremely high measurement accuracy and resolution. In high-precision mode, its pressure resolution is ±0.006 hPa (about 5 cm of altitude). Its typical relative accuracy is about ±0.12 hPa, and nonlinearity error is around ±0.06 hPa, and it provides a 24-bit digital output for fine sensitivity. Such high resolution can detect height changes that are barely noticeable.
Low Power Design
The WF282A’s low-power design is ideal for portable applications. Typically at 1 Hz sampling the current is about 2.7 μA; in high-precision mode around 60 μA, in low-power mode only 3 μA, and standby current below 1 μA. These ultra-low power features make the sensor great for battery-powered devices that need long runtime.
Compact Packaging and Interface Options
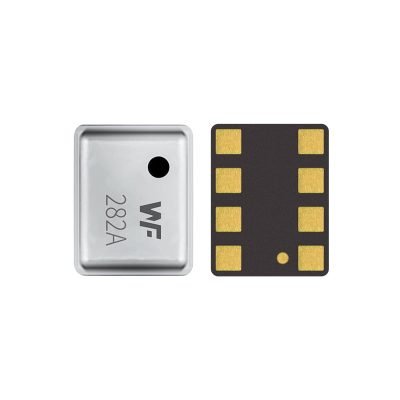
The WF282A comes in a tiny 8-pad LGA package measuring just 2.0×2.5×0.95 mm, making it extremely compact. It communicates with a host via a digital I2C or SPI interface and even offers an optional interrupt output to simplify data retrieval. There is a small hole on top of the package serving as the pressure port, which must be kept clear of blockage during design and assembly.
FIFO Buffer and Data Processing
The WF282A includes on-chip FIFO buffering and data processing. Its built-in FIFO can store up to 32 measurement samples, so the host can read multiple values at once and then sleep longer to reduce overall power consumption. The sensor also supports configurable digital filtering (such as IIR filters) and oversampling modes, which suppress noise while maintaining a high sample rate. These internal functions improve measurement reliability and simplify software processing.
Key Points for Soldering and Mounting the Sensor in the Device
Footprint Layout and PCB Design
When designing the PCB layout, follow the WF282A’s 8-pad LGA footprint, matching pad size to the device. Typically, leave an opening around the pressure port and use solder-mask dams on the pads to prevent solder from flowing into the port. Also ensure even routing to the GND and VCC pads to minimize thermal stress, and you may add copper pours on inner layers for better thermal stability. Avoid trapping air pockets or trenches under the sensor, as trapped air can dampen pressure transmission. Make sure the PCB pads are flat so that the sensor’s underside makes good contact.
Soldering and Reflow
For soldering, use the recommended lead-free reflow process: ramp-up at no more than 3°C/s, with a peak around 260°C, and dwell for 60–150 seconds above 217°C. After reflow, let the board cool naturally and avoid rapid cooling. Usually only one reflow cycle is needed per sensor to avoid repeated heating. For rework, use a low-temperature soldering iron quickly to minimize heating time. Use ESD precautions to protect the sensor, and inspect the joints to ensure there are no cold joints or solder bridges.
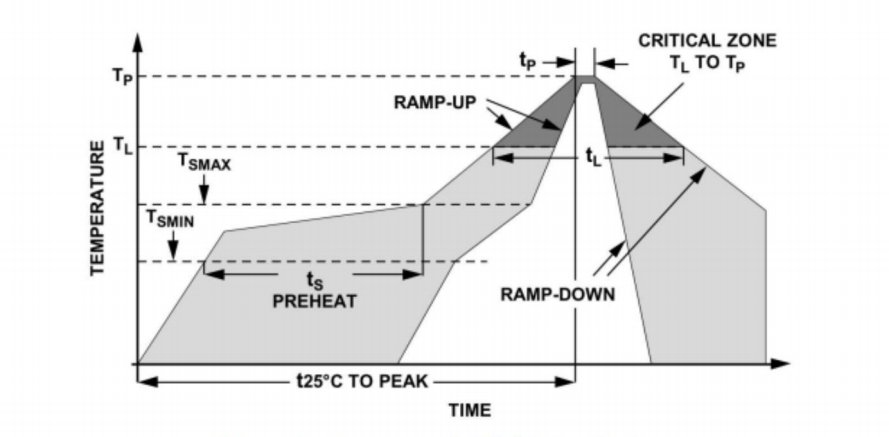
Pressure Port Protection
After soldering, inspect and clean the port to ensure no solder or debris is blocking the pressure opening. If waterproofing is needed, use a sealed enclosure with a breathable membrane so the sensor port is exposed to the atmosphere but not to water. Avoid potting compounds or epoxies that would cover the port; instead use O-rings or gaskets to seal the housing, ensuring the port remains vented.
Mechanical Mounting and Protection
The sensor is held in place by its solder pads and usually needs no extra mechanical support. In a wearable device, however, the enclosure should provide shock protection to dampen impacts and vibrations. If adhesive is needed, apply it only around the edges and avoid covering the pressure port or pads. Never mount the sensor directly onto a flexible surface.
Testing Procedures and Recommended Instruments/Methods Before Mass Production
Functional and Calibration Testing
Before mass production, it is recommended to perform functional verification and calibration tests on each batch of sensors. The typical procedure includes: 1) place the sensor at standard atmospheric pressure (~1013 hPa) and read the output to check the offset; 2) use a precision pressure source or deadweight tester to apply pressures at multiple points (e.g., 900 hPa, 1100 hPa) to verify linearity and sensitivity; 3) use an automated test system to read sensor data via I2C/SPI in batch and repeat these tests under different temperature conditions to assess temperature drift. You can also perform field tests at known altitude points (such as an altitude calibration tower) for further accuracy verification.
Environmental and Reliability Tests
Tests should also include environmental and reliability items: do temperature cycling in a climate chamber to evaluate output drift at extreme temperatures; perform humidity tests to observe the sensor’s behavior in moist environments. Conduct water immersion or pressure cycling tests to verify sealing and durability, for example by placing the device in a water tank or pressure chamber to simulate repeated dives. Vibration and shock tests help evaluate the reliability of the sensor and the overall device structure in dynamic conditions.
Recommended Test Instruments/Methods
Recommended test equipment and methods include:
Precision pressure calibrator: e.g. Fluke 716 or Mensor CPC100, to provide programmable air or water pressure.
Thermal/humidity chamber: to test the effects of temperature and humidity on the sensor.
Automated test board: with MCU or FPGA to batch read/write sensor registers via I2C/SPI and record data.
Water pressure test setup: a pressure water tank or pressure chamber to simulate different diving depths.
Power analyzer or oscilloscope: to monitor the sensor’s sampling timing and current draw.
Reference standards: use calibrated standard pressure sensors to verify measurement results.
Mode Switching Algorithms and Environmental Compensation Factors
Trigger for Mode Switching
You must determine when to switch from altitude mode to diving mode. A simple strategy is to declare a dive when the device detects a rapid pressure rise beyond the normal atmospheric range (for example, staying above 1100 hPa). To avoid false triggers, you can require the pressure to exceed the threshold for a sustained time or use a humidity sensor or other water-detection mechanism. The user interface can also offer a manual mode switch as a backup if automatic detection fails.
Altitude Calculation Algorithm
In altitude mode, use the barometric formula to convert pressure to altitude. A common formula is h ≈ 44330 × (1 − (P/Po)^0.1903), where Po is the sea-level reference pressure. In practice, use the reference pressure measured at startup (or provided by GPS altitude data) as Po, and apply the sensor’s temperature reading for compensation. You can use a moving average or Kalman filter to smooth the output and reduce noise.
Diving Calculation Algorithm
In diving mode, calculate depth from hydrostatic pressure: D ≈ (P − P0)/(ρ·g). Here P0 is the atmospheric pressure at the surface, which can be recorded at the start of the dive. The density ρ of freshwater is about 1000 kg/m³ (a bit higher for seawater), and temperature affects density as well. A simplified rule is that every 100 hPa corresponds to about 1 meter of freshwater depth. The system should continuously measure pressure and update the depth in real-time.
Environmental Compensation Factors
To improve accuracy, compensate for environmental factors. The sensor’s built-in temperature reading can correct for pressure drift due to temperature changes. In altitude mode, you may consider the effect of humidity on air density. In diving mode, account for the effect of water temperature and salinity on density (for example, seawater density is slightly higher than freshwater). Additionally, applying a low-pass filter or averaging to the pressure data can remove short-term disturbances and stabilize the results.
Summary
Using a MEMS absolute pressure sensor to measure both altitude and dive depth in one device requires addressing different pressure ranges, accuracy needs, and algorithms for each mode. The WF282A, with its high accuracy, low power, compact package, and built-in FIFO, provides a strong hardware foundation for dual-mode measurement. In design, attention must be paid to PCB layout and soldering, keeping the pressure port clear, and thorough testing and calibration. By employing the correct environmental compensation (such as for temperature and density), the device can seamlessly switch between altitude and diving modes and achieve precise measurements.
The above introduction only scratches the surface of the applications of pressure sensor technology. We will continue to explore the different types of sensor elements used in various products, how they work, and their advantages and disadvantages. If you’d like more detail on what’s discussed here, you can check out the related content later in this guide. If you are pressed for time, you can also click here to download the details of this guides air pressure sensor product PDF data.
For more information on other sensor technologies, please visit our sensors page.
The WF282A sensor seems to be an excellent choice for applications requiring high precision and low power consumption. Its compact size and digital interface options make it versatile for various designs. The built-in FIFO and filtering features enhance both performance and efficiency. Proper PCB layout considerations are crucial for optimal functionality. Have you tested this sensor in extreme environmental conditions to ensure its accuracy remains consistent?
The sensor has been tested under extreme environmental conditions to virtually guarantee consistent accuracy