ในโลกที่มีการพัฒนาอย่างรวดเร็วในปัจจุบัน, เซ็นเซอร์มีบทบาทสำคัญในการเปลี่ยนข้อมูลดิบให้เป็นข้อมูลเชิงลึกที่สามารถดำเนินการได้ในอุตสาหกรรม. ในหมู่เหล่านี้, เซ็นเซอร์ความดัน Piezoresistive ได้กลายเป็นเทคโนโลยีที่สำคัญด้วยแอพพลิเคชั่นที่ครอบคลุมตั้งแต่ยานยนต์และการดูแลสุขภาพไปจนถึงอุปกรณ์อิเล็กทรอนิกส์สำหรับผู้บริโภคและระบบอัตโนมัติอุตสาหกรรม. บทความนี้ดำดิ่งสู่พื้นฐานและการใช้งานจริงของเซ็นเซอร์เหล่านี้, สรุปแง่มุมทางเทคนิคของพวกเขา, และอธิบายว่าทำไมพวกเขาถึงมีความสำคัญในเทคโนโลยีที่ทันสมัย.
แคตตาล็อก
ทำความเข้าใจกับเซ็นเซอร์ความดัน piezoresistive
เมมส์ (ระบบกลไกไฟฟ้าขนาดเล็ก) เทคโนโลยีได้เปลี่ยนการออกแบบเซ็นเซอร์ผ่านการย่อขนาดและการผลิตที่ประหยัดต้นทุน. ในบรรดาเซ็นเซอร์ประเภทต่างๆ, เซ็นเซอร์ความดัน Piezoresistive มีการเฉลิมฉลองสำหรับความสามารถในการวัดการเปลี่ยนแปลงแรงดันเล็กน้อยในการใช้งานที่หลากหลาย. ในส่วนนี้, เราสำรวจหลักการทำงาน, ประโยชน์, และความแตกต่างระหว่างเซ็นเซอร์ piezoresistive และคู่หู piezoelectric ของพวกเขา.
เซ็นเซอร์ piezoresistive ทำงานอย่างไร?
เซ็นเซอร์ Piezoresistive ทำงานบนหลักการที่ความต้านทานทางไฟฟ้าของการเปลี่ยนแปลงของวัสดุเมื่อใช้ความเค้นเชิงกลถูกนำไปใช้. ในเซ็นเซอร์ MEMS, คริสตัลซิลิกอนที่เจือทำหน้าที่เป็นองค์ประกอบการตรวจจับ. เมื่อใช้แรงดัน, การเสียรูปในซิลิกอนเปลี่ยนความต้านทานในวิธีที่คาดเดาได้. การเปลี่ยนแปลงนี้จะถูกวัดโดยใช้การกำหนดค่าเช่นสะพาน Wheatstone, องค์ประกอบสำคัญในการรับรองการอ่านที่แม่นยำ.
ข้อได้เปรียบของผล piezoresistive อยู่ในความสอดคล้องของมัน. ไม่เหมือนเซ็นเซอร์ประเภทอื่น ๆ, เซ็นเซอร์เหล่านี้ให้การทำซ้ำได้ดีเยี่ยม, ซึ่งมีความสำคัญในการเรียกร้องแอปพลิเคชันเช่นอุปกรณ์การแพทย์หรือระบบยานยนต์.
ผล piezoresistive ใน mems คืออะไร?
ผล piezoresistive ใน MEMs เกี่ยวข้องกับการเปลี่ยนแปลงของความต้านทานไฟฟ้าของวัสดุเซมิคอนดักเตอร์เมื่ออยู่ภายใต้ความเครียดเชิงกล. ปรากฏการณ์นี้, ซึ่งได้รับการศึกษาอย่างกว้างขวาง, เป็นกุญแจสำคัญในการทำความเข้าใจพฤติกรรมของเซ็นเซอร์ภายใต้เงื่อนไขการปฏิบัติงานที่แตกต่างกัน. ในทางปฏิบัติ, ผู้ผลิตควบคุมยาสลบของซิลิคอนเพื่อปรับความไวและบรรลุความแม่นยำในการวัดสูง.
ตัวอย่างในโลกแห่งความเป็นจริงจากสาขาของเราแสดงให้เห็นว่าวิศวกรรมอย่างรอบคอบขององค์ประกอบ piezoresistive นำไปสู่เซ็นเซอร์ที่มีประสิทธิภาพที่ทำงานได้อย่างน่าเชื่อถือแม้ในสภาพแวดล้อมที่รุนแรง. เครื่องมือเช่นซอฟต์แวร์การจำลองขั้นสูงและเทคนิคการปลูกถ่ายไอออนที่แม่นยำนั้นถูกนำมาใช้เป็นประจำในระหว่างการพัฒนาเพื่อทำนายประสิทธิภาพของเซ็นเซอร์และตรวจสอบให้แน่ใจว่าสอดคล้องกับมาตรฐานที่เข้มงวด.
เซ็นเซอร์ความดัน piezoelectric ทำงานอย่างไร?
แม้ว่าเราจะให้ความสำคัญกับเทคโนโลยี piezoresistive, การทำความเข้าใจเซ็นเซอร์ความดัน piezoelectric เป็นสิ่งจำเป็นเนื่องจากการใช้งานเสริมของพวกเขา. เซ็นเซอร์ Piezoelectric ทำงานบนหลักการที่แตกต่างกัน: วัสดุบางอย่างสร้างประจุไฟฟ้าเมื่อมีการเปลี่ยนรูปแบบกลไก. ประจุนี้สามารถวัดได้เพื่อระบุความดันที่ใช้. ในขณะที่เซ็นเซอร์ทั้งสองประเภทมีค่า, เซ็นเซอร์ความดัน Piezoelectric มักจะเก่งในการใช้งานที่ต้องใช้เวลาตอบสนองแบบไดนามิกมาก, เช่นการสั่นสะเทือนและการตรวจจับเสียง.
เซ็นเซอร์ piezoelectric วัดอะไร?
เซ็นเซอร์ Piezoelectric มีช่วงการวัดที่กว้าง. ส่วนใหญ่จะใช้ในการวัดพารามิเตอร์แบบไดนามิกเช่นการสั่นสะเทือน, กองกำลัง, และผลกระทบ. ความหลากหลายของเซ็นเซอร์ piezoelectric, รวมถึงประเภทเช่นเซ็นเซอร์ทรานสดิวเซอร์ Piezoelectric และเซ็นเซอร์โหลด Piezoelectric, ทำให้พวกเขาเป็นตัวเลือกยอดนิยมในฟิลด์เช่นการตรวจจับความผิดพลาดยานยนต์, เทคโนโลยีที่สวมใส่ได้, และการตรวจสอบอุตสาหกรรม.
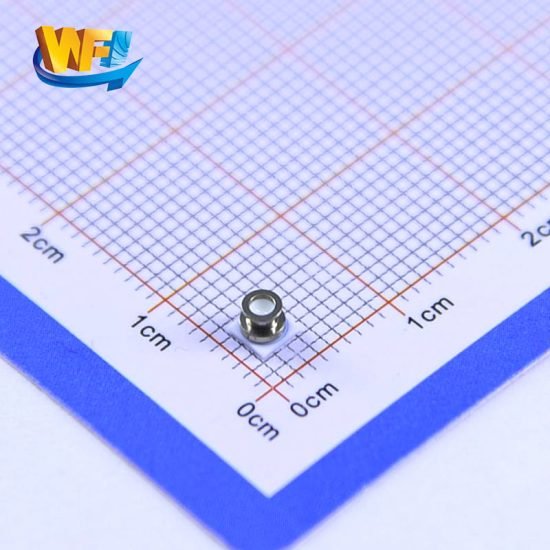
หากคุณสนใจที่จะทำความเข้าใจเพิ่มเติมเกี่ยวกับ [เซ็นเซอร์ piezoelectric วัดอะไร?], การสำรวจการบูรณาการของเอฟเฟกต์ piezoelectric ทั้งในเซ็นเซอร์ความดันและการเร่งความเร็วขอแนะนำอย่างยิ่งสำหรับมุมมองที่ครอบคลุมของความสามารถของเซ็นเซอร์.
ความแตกต่างระหว่างเซ็นเซอร์ piezoelectric และ piezoresistive
ในขณะที่เซ็นเซอร์ทั้งสองประเภทแปลงแรงทางกลเป็นสัญญาณไฟฟ้า, พวกเขาแตกต่างกันในวิธีสำคัญ. เซ็นเซอร์ Piezoresistive ให้อย่างต่อเนื่อง, การอ่านที่ทำซ้ำได้สูงและเหมาะสมกว่าสำหรับแอปพลิเคชันที่การวัดแบบคงที่มีความสำคัญ, เช่นในการตรวจสอบเครื่องยนต์ยานยนต์หรืออุปกรณ์การแพทย์. ในทางกลับกัน, เซ็นเซอร์ Piezoelectric Excel ในสภาพแวดล้อมแบบไดนามิกซึ่งจำเป็นต้องมีการเปลี่ยนแปลงสัญญาณอย่างรวดเร็ว.
ด้านเทคนิคและกระบวนการผลิต
ในส่วนนี้, เราเจาะลึกลงไปในความซับซ้อนของการผลิต MEMS, อธิบายความสำคัญของการออกแบบและการสอบเทียบส่วนประกอบ, และตรวจสอบว่าปัจจัยอุณหภูมิและความเครียดได้รับการจัดการเพื่อรักษาความแม่นยำของเซ็นเซอร์.
MEMS การผลิตและข้อได้เปรียบในการออกแบบ
เทคโนโลยี MEMS ใช้ประโยชน์จากเทคนิคการผลิตเซมิคอนดักเตอร์เช่น photolithography, การแกะสลัก, และการฝังไอออนเพื่อสร้างเซ็นเซอร์ความดันในระดับกล้องจุลทรรศน์. สิ่งนี้ไม่เพียง แต่ผลักดันต้นทุนต่อหน่วยเท่านั้น แต่ยังช่วยให้สามารถผลิตได้ในปริมาณมากด้วยคุณภาพที่สอดคล้องกัน.
ข้อได้เปรียบที่สำคัญของการใช้ MEMS สำหรับการผลิตเซ็นเซอร์คือความสามารถในการรวมเซ็นเซอร์จำนวนมากบนเวเฟอร์ซิลิกอนเดี่ยว. การบูรณาการนี้ช่วยปรับปรุงความสอดคล้องของประสิทธิภาพในขณะที่สร้างความมั่นใจในการปรับขนาดสำหรับแอพพลิเคชั่นอุตสาหกรรมขนาดใหญ่.
ไดอะแฟรมซิลิกอนและสะพานวีทสโตน
หัวใจของเซ็นเซอร์ความดัน piezoresistive mems เป็นไดอะแฟรมซิลิคอน - บาง ๆ, เมมเบรนที่มีความยืดหยุ่นซึ่งเปลี่ยนรูปภายใต้แรงกดดัน. ควบคู่ไปกับสะพาน Wheatstone, การออกแบบนี้แปลงการเสียรูปแบบเชิงกลเป็นสัญญาณไฟฟ้าที่สามารถวัดได้อย่างแม่นยำ.
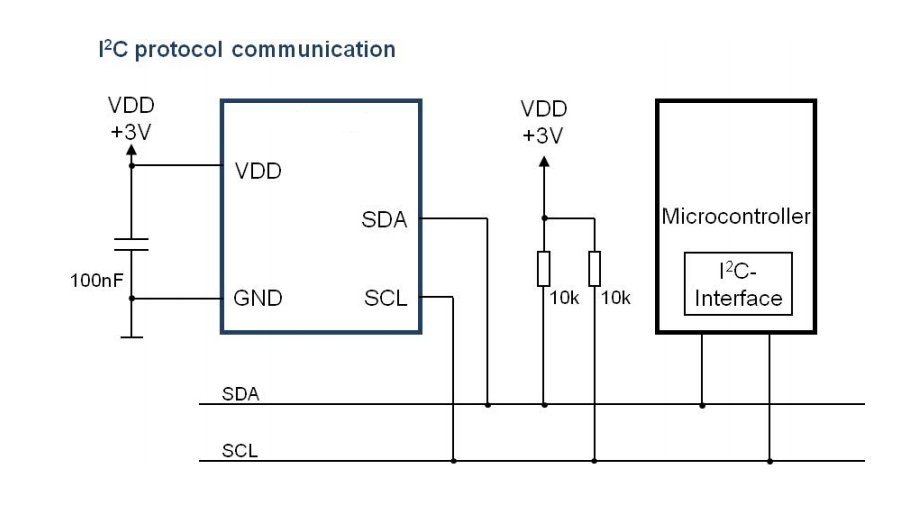
ผู้ผลิตอย่างรอบคอบวิศวกรชุดนี้เพื่อลด hysteresis และชดเชยดริฟท์. เป็นผลให้, เซ็นเซอร์แสดงประสิทธิภาพที่เชื่อถือได้ในช่วงแรงกดดันที่เพิ่มขึ้น, ทำให้เหมาะสำหรับแอพพลิเคชั่นเช่นยานยนต์และอุปกรณ์การแพทย์.
ผลกระทบอุณหภูมิ: TCR และ TCS
ความผันผวนของอุณหภูมิอาจมีผลต่อประสิทธิภาพของเซ็นเซอร์ความดัน. ปัจจัยสำคัญสองประการที่นี่คือค่าสัมประสิทธิ์อุณหภูมิของความต้านทาน (TCR) และค่าสัมประสิทธิ์อุณหภูมิของช่วง (TCS). TCR ช่วยในการทำความเข้าใจว่าความต้านทานไฟฟ้าเปลี่ยนแปลงอย่างไรกับอุณหภูมิ, ในขณะที่ TCS ระบุว่าความไวของเซ็นเซอร์ได้รับผลกระทบจากการเปลี่ยนแปลงของอุณหภูมิอย่างไร.
ใช้เทคนิคการสอบเทียบและการชดเชยที่แม่นยำในระหว่างการผลิตเพื่อให้แน่ใจว่าเซ็นเซอร์ยังคงเชื่อถือได้และแม่นยำในช่วงอุณหภูมิที่กว้าง.
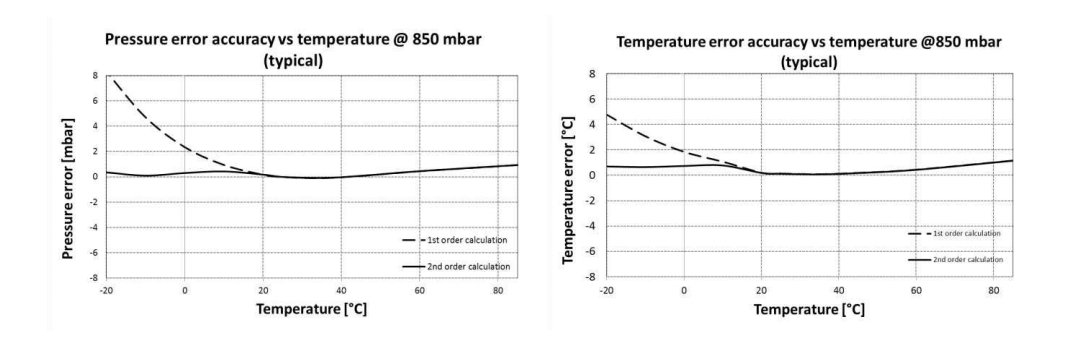
สร้างความมั่นใจในความแม่นยำและความมั่นคง
ความแม่นยำของเซ็นเซอร์ความดันเป็นสิ่งสำคัญยิ่ง, โดยเฉพาะอย่างยิ่งในการใช้งานที่สำคัญ. กระบวนการสอบเทียบ, มักจะได้รับความช่วยเหลือจาก ASIC แบบบูรณาการ (วงจรรวมเฉพาะแอปพลิเคชัน), ช่วยในการลดข้อผิดพลาดทั้งหมดโดยการชดเชยความไม่เป็นเชิงเส้น, การตีโพยตีพาย, และข้อผิดพลาดเล็กน้อยอื่น ๆ.
ผู้ผลิตยังทำการทดสอบอย่างเข้มงวดเพื่อยืนยันว่าเซ็นเซอร์เป็นไปตามมาตรฐานสากลเพื่อความแม่นยำและการทำซ้ำ. การมุ่งเน้นที่ความแม่นยำนี้ช่วยให้มั่นใจได้ว่าเซ็นเซอร์สามารถตรวจสอบและควบคุมกระบวนการในอุตสาหกรรมเดิมพันสูงได้อย่างน่าเชื่อถือ.
ความเครียดและการพิจารณาการดริฟท์ชดเชย
ความเครียดเชิงกลภายนอก - ไม่ว่าจะมาจากบรรจุภัณฑ์, กระบวนการประกอบ, หรือโหลดการดำเนินงาน - ทำให้การเปลี่ยนแปลงประสิทธิภาพของเซ็นเซอร์เล็กน้อยเมื่อเวลาผ่านไป. ปรากฏการณ์นี้, รู้จักกันในชื่อออฟเซ็ตดริฟท์, ได้รับการจัดการอย่างรอบคอบผ่านการออกแบบบรรจุภัณฑ์ที่แข็งแกร่งและกลไกการบรรเทาความเครียด.
การสร้างความมั่นใจว่าการดริฟท์ที่เกิดจากความเครียดน้อยที่สุดเป็นสิ่งสำคัญในการรักษาความมั่นคงในระยะยาวและความน่าเชื่อถือของเซ็นเซอร์. มาตรการเหล่านี้ไม่เพียง แต่ยืดอายุการใช้งานของเซ็นเซอร์เท่านั้น แต่ยังป้องกันความล้มเหลวของระบบในการใช้งานที่ละเอียดอ่อน.
แอปพลิเคชั่นที่ใช้งานได้จริงในอุตสาหกรรม
เซ็นเซอร์ความดัน piezoresistive มีการใช้งานที่หลากหลายซึ่งครอบคลุมหลายอุตสาหกรรม. ในส่วนนี้, เราตรวจสอบกรณีการใช้งานเฉพาะ, เน้นว่าเซ็นเซอร์เหล่านี้มีส่วนร่วมในนวัตกรรมและความปลอดภัยในสาขาต่างๆ.

ยานยนต์และการขนส่ง
ในภาคยานยนต์, เซ็นเซอร์ความดันถูกนำมาใช้อย่างกว้างขวางสำหรับการจัดการเครื่องยนต์, การควบคุมการปล่อยมลพิษ, และระบบความปลอดภัย. ตัวอย่างเช่น, เซ็นเซอร์ตรวจสอบความดันลมยาง, ช่วยรักษาประสิทธิภาพการใช้เชื้อเพลิงและลดความเสี่ยงของการเกิดอุบัติเหตุ. ในระบบการช่วยเหลือผู้ขับขี่ขั้นสูง (Adas), เซ็นเซอร์มีส่วนร่วมในคุณสมบัติต่าง ๆ เช่นการหลีกเลี่ยงการชนและการควบคุมความเร็วคงที่.
นอกจากนี้, บริษัท ยานยนต์พึ่งพาเซ็นเซอร์เหล่านี้เพื่อตรวจสอบแรงดันไอเสียและการบริโภค. การบูรณาการนี้ช่วยเพิ่มประสิทธิภาพของเครื่องยนต์และลดการปล่อยมลพิษ - ลำดับความสำคัญที่เพิ่มขึ้นในการขนส่งที่ทันสมัย.
การแพทย์และการดูแลสุขภาพ
ความแม่นยำของพวกเขาทำให้มั่นใจได้ว่าปริมาณและแรงกดดันจะได้รับการบำรุงรักษาภายในขอบเขตที่ปลอดภัย, ดังนั้นการปกป้องสุขภาพของผู้ป่วย.
ในสาขาการแพทย์, ความแม่นยำและความน่าเชื่อถือของเซ็นเซอร์ความดัน piezoresistive เป็นสิ่งจำเป็น. พวกเขาใช้ในการใช้งานที่สำคัญเช่นจอภาพความดันโลหิตและเครื่องช่วยหายใจ. ในระหว่างขั้นตอนการแพทย์เช่น angioplasty, เซ็นเซอร์เหล่านี้นำทางแพทย์โดยให้ข้อเสนอแนะแบบเรียลไทม์เกี่ยวกับระดับความดันภายในหลอดเลือดแดง.
อุปกรณ์อิเล็กทรอนิกส์สำหรับผู้บริโภคและอุปกรณ์สมาร์ท
สินค้าอุปโภคบริโภคที่ทันสมัยขึ้นอยู่กับเซ็นเซอร์ที่มีความซับซ้อนมากขึ้นเรื่อย ๆ. อุปกรณ์เช่นสมาร์ทโฟน, เครื่องติดตามออกกำลังกายที่สวมใส่ได้, และแม้แต่ระบบอัตโนมัติในบ้านก็ยังได้รับประโยชน์จากการวัดแรงดันที่แม่นยำ. MEMS accelerometers และ gyroscopes - เกี่ยวข้องกับหัวข้อของเรา - เป็นเรื่องธรรมดาในอุปกรณ์เหล่านี้และช่วยปรับปรุงประสบการณ์ผู้ใช้โดยการเปิดใช้งานการรับรู้ท่าทางและการติดตามการปฐมนิเทศ.
เนื่องจากอุปกรณ์อิเล็กทรอนิกส์ของผู้บริโภครวมอยู่ในระบบนิเวศของสมาร์ทโฮม, ความน่าเชื่อถือและการย่อขนาดของเซ็นเซอร์ยิ่งมีความสำคัญยิ่งขึ้น.
ระบบอัตโนมัติอุตสาหกรรมและการควบคุมกระบวนการ
การตรวจสอบความดันที่แม่นยำในสภาพแวดล้อมเหล่านี้ไม่เพียง แต่เกี่ยวกับการเพิ่มประสิทธิภาพกระบวนการเท่านั้น แต่ยังเกี่ยวกับการป้องกันความล้มเหลวที่มีค่าใช้จ่ายสูง.
อุตสาหกรรมเช่นการผลิต, เครื่องปรับอากาศ, และการควบคุมกระบวนการขึ้นอยู่กับเซ็นเซอร์ความดันที่แม่นยำอย่างมากเพื่อให้แน่ใจว่ามีเสถียรภาพในการปฏิบัติงานและความปลอดภัย. เซ็นเซอร์มีบทบาทสำคัญในการตรวจสอบและควบคุมทุกอย่างตั้งแต่พลวัตของเหลวในท่อไปจนถึงการรักษาสภาพแวดล้อมที่แม่นยำในโรงงานผลิต.
แอปพลิเคชั่นดำน้ำและกลางแจ้ง
อุตสาหกรรมการดำน้ำใช้ประโยชน์จากเซ็นเซอร์ความดันเพื่อตรวจสอบความลึกใต้น้ำและให้ความมั่นใจกับความปลอดภัยของนักดำน้ำ. เนื่องจากความดันบรรยากาศลดลงตามความลึก, เซ็นเซอร์ให้ข้อมูลที่สำคัญที่ช่วยให้นักดำน้ำคำนวณอัตราการขึ้นและอัตราการสืบเชื้อสายได้อย่างถูกต้อง. หลักการที่คล้ายกันใช้กับแอปพลิเคชันกลางแจ้ง, เช่น Altimeters ที่ใช้ในการเดินป่าระดับสูงหรือกีฬาสันทนาการ.
สำหรับผู้ที่ชื่นชอบและมืออาชีพ, การตรวจสอบความดันที่เชื่อถือได้เป็นกุญแจสำคัญต่อความปลอดภัยและประสิทธิภาพ.
ความก้าวหน้า
ก้าวอย่างรวดเร็วของนวัตกรรมในเทคโนโลยีเซ็นเซอร์ยังคงเปิดแอพพลิเคชั่นใหม่และปรับปรุงการออกแบบที่มีอยู่.
แนวโน้มที่เกิดขึ้นใหม่ในเทคโนโลยีเซ็นเซอร์ MEMS
ความก้าวหน้าล่าสุดในการผลิต MEMS ได้นำไปสู่เซ็นเซอร์ที่มีขนาดเล็กลง, คุ้มค่ามากขึ้น, และเชื่อถือได้มากขึ้น. นวัตกรรมในด้านวิทยาศาสตร์วัสดุและเทคนิคการสร้างไมโครฟิล์มกำลังผลักดันการปรับปรุงความไวของเซ็นเซอร์และช่วงการทำงาน. ความก้าวหน้าเหล่านี้มีความสำคัญในการตอบสนองความต้องการที่เพิ่มขึ้นของอุตสาหกรรมสมัยใหม่ตั้งแต่ยานยนต์ไปจนถึงอุปกรณ์อิเล็กทรอนิกส์สำหรับผู้บริโภค.
การรวมเซ็นเซอร์ MEMS เข้ากับแพลตฟอร์ม IoT
ด้วยการขยายตัวอย่างรวดเร็วของ Internet of Things (ไอโอที), การรวมเซ็นเซอร์เข้ากับเครือข่ายที่เชื่อมต่อกำลังกลายเป็นสิ่งจำเป็น. MEMS เซ็นเซอร์ความดัน, ด้วยขนาดเล็กและการใช้พลังงานต่ำ, เป็นผู้สมัครที่เหมาะสำหรับการใช้งาน IoT. พวกเขาให้ข้อมูลแบบเรียลไทม์ที่สามารถใช้ในการปรับเปลี่ยนทันทีในการตั้งค่าอุตสาหกรรม, บ้านอัจฉริยะ, และแม้แต่ในแอปพลิเคชันยานยนต์.
นวัตกรรมในการผลิตต้นทุนต่ำ
การลดต้นทุนการผลิตโดยไม่ส่งผลกระทบต่อคุณภาพเป็นจุดสนใจหลักในตลาดเซ็นเซอร์. ความสามารถในการประดิษฐ์เซ็นเซอร์หลายพันตัวในเวเฟอร์ซิลิกอนเดี่ยวเป็นหนึ่งในปัจจัยประหยัดต้นทุนที่สำคัญที่สุดที่เกี่ยวข้องกับเทคโนโลยี MEMS. เมื่อกระบวนการผลิตมีความคล่องตัวมากขึ้น, จุดราคาโดยรวมสำหรับเซ็นเซอร์คุณภาพสูงคาดว่าจะลดลงต่อไป. แนวโน้มนี้ทำให้ง่ายขึ้นสำหรับองค์กรขนาดเล็กและขนาดย่อมในการใช้เทคโนโลยีเซ็นเซอร์ขั้นสูง.
แนวโน้มในอนาคตและการคาดการณ์ตลาด
การวิจัยตลาดคาดการณ์ว่าอุตสาหกรรมเซ็นเซอร์ความดันจะยังคงเติบโตอย่างมีนัยสำคัญ, ถึงเกือบ 24.5 พันล้านดอลลาร์โดย 2028. การฉายภาพนี้สะท้อนถึงความต้องการที่เพิ่มขึ้นในอุตสาหกรรมต่าง ๆ เนื่องจากแอปพลิเคชันเซ็นเซอร์ยังคงขยายตัว. นวัตกรรมอย่างต่อเนื่องทั้งในการออกแบบและการใช้งานมีแนวโน้มที่จะผลักดันการใช้เซ็นเซอร์ความดัน MEMS ในพื้นที่ตั้งแต่การดูแลสุขภาพไปจนถึงความปลอดภัยของยานยนต์.
บทสรุป
เคล็ดลับการปฏิบัติ:
การเลือก: เมื่อเลือกเซ็นเซอร์, พิจารณาทั้งช่วงความดันในการดำเนินงานและสิ่งแวดล้อม. เช่น, แอปพลิเคชันที่มีการแปรผันของอุณหภูมิสูงอาจต้องใช้เซ็นเซอร์ที่มีการชดเชย TCR และ TCS ที่แข็งแกร่ง.
การติดตั้ง: ปฏิบัติตามแนวทางของผู้ผลิตอย่างรอบคอบเพื่อลดความเครียดและชดเชยการดริฟท์ระหว่างการติดตั้ง. บรรจุภัณฑ์ที่เหมาะสมไม่เพียง แต่ปกป้องเซ็นเซอร์เท่านั้น แต่ยังช่วยให้มั่นใจได้ถึงความมั่นคงในระยะยาว.
การสอบเทียบ: การสอบเทียบเป็นประจำเป็นสิ่งจำเป็นในการรักษาความถูกต้อง. ใช้เครื่องมือการสอบเทียบขั้นสูงและ ASICS ออนบอร์ดเมื่อพร้อมใช้งานเพื่อปรับแต่งเซ็นเซอร์แบบปรับแต่ง.
การรวมเข้าด้วยกัน: สำหรับแอปพลิเคชัน IoT, ตรวจสอบให้แน่ใจว่าเซ็นเซอร์เข้ากันได้กับแพลตฟอร์มดิจิตอลที่มีอยู่ของคุณ. การรวมนี้สามารถให้ข้อมูลเชิงลึกข้อมูลแบบเรียลไทม์ซึ่งมีความสำคัญต่อการบำรุงรักษาทำนายและการควบคุมกระบวนการ.
การพิสูจน์ในอนาคต: จับตาดูแนวโน้มที่เกิดขึ้นใหม่, เช่นการเก็บเกี่ยวพลังงานและการย่อขนาดเซ็นเซอร์, ซึ่งอาจให้คุณค่าเพิ่มเติมเมื่อแอปพลิเคชันของคุณมีวิวัฒนาการ.
เราหวังว่าบทความนี้จะให้ความเข้าใจที่ชัดเจนเกี่ยวกับ MEMS piezoresistive เซ็นเซอร์ความดัน - จากหลักการทำงานและกระบวนการผลิตไปจนถึงการใช้งานจริงและศักยภาพในอนาคตของพวกเขา.
โดยใช้ประโยชน์จากความรู้ด้านเทคนิคที่ลึกซึ้งและข้อมูลเชิงลึกในโลกแห่งความจริงที่ใช้ร่วมกันที่นี่, คุณสามารถเลือกและใช้โซลูชันเซ็นเซอร์ MEMS อย่างมั่นใจที่เหมาะกับความต้องการของอุตสาหกรรมของคุณ. อยากรู้อยากเห็นและสำรวจโลกการเปลี่ยนแปลงของเทคโนโลยีเซ็นเซอร์.
บทนำข้างต้นเป็นเพียงรอยขีดข่วนพื้นผิวของการใช้งานของเทคโนโลยีเซ็นเซอร์ความดัน. เราจะสำรวจองค์ประกอบเซ็นเซอร์ประเภทต่าง ๆ ที่ใช้ในผลิตภัณฑ์ต่าง ๆ, พวกเขาทำงานอย่างไร, และข้อดีและข้อเสียของพวกเขา. หากคุณต้องการรายละเอียดเพิ่มเติมเกี่ยวกับสิ่งที่กล่าวถึงที่นี่, คุณสามารถตรวจสอบเนื้อหาที่เกี่ยวข้องในภายหลังในคู่มือนี้. หากคุณถูกกดเวลา, คุณสามารถคลิกที่นี่เพื่อดาวน์โหลดรายละเอียดของคู่มือนี้ ข้อมูลผลิตภัณฑ์เซ็นเซอร์ความดันอากาศ.
สำหรับข้อมูลเพิ่มเติมเกี่ยวกับเทคโนโลยีเซ็นเซอร์อื่น ๆ, โปรด เยี่ยมชมหน้าเซ็นเซอร์ของเรา.