แคตตาล็อก
Absolute pressure sensors serve critical pressure monitoring and control functions in laser systems, directly determining operational stability and processing quality. These sensors provide precise pressure feedback through real-time monitoring of laser cavities, gas supply systems, and cooling circuits, ensuring optimal equipment performance. MEMS technology advancement has equipped modern absolute pressure sensors with high accuracy, rapid response, and long-term stability, making them irreplaceable core components in laser machine pressure control systems.
1. Core Working Principles of Absolute Pressure Sensors
Pressure Detection Mechanism and Signal Conversion
Absolute pressure sensors utilize piezoresistive or piezoelectric principles. When laser machine internal pressure changes, sensor elements produce corresponding resistance or charge variations. Piezoresistive sensors based on semiconductor material effects change electrical resistance under pressure, outputting signals proportional to pressure. This detection method offers excellent linearity and temperature stability, particularly suitable for precision-demanding laser equipment. Built-in signal conditioning circuits amplify weak pressure signals and convert them to standard voltage or current outputs for easy integration with laser control systems. Flush-mount design prevents sensor clogging, ensuring maintenance-free operation.
Multi-Mode Detection Functions and Response Characteristics
Modern absolute pressure sensors integrate multiple detection modes including pressure detection, adsorption detection, leak detection, and window detection modes, adapting to various laser machine operating conditions. Pressure detection provides basic measurement functionality with millisecond response times, meeting rapid pressure change monitoring requirements. Adsorption mode specifically detects gas adsorption situations, preventing abnormal gas concentrations in laser cavities. Leak mode promptly discovers system leaks, avoiding pressure loss affecting laser output quality. Window mode allows users to set monitoring ranges, automatically triggering alarms when exceeding preset windows. These diverse detection modes enable single sensors to replace multiple specialized sensors, simplifying system design.
Precision Control and Calibration Technology
Absolute pressure sensor measurement accuracy directly impacts laser machine performance, with high-end sensors achieving 0.1% ความแม่นยำเต็มรูปแบบ. To ensure long-term measurement accuracy, sensors employ temperature compensation and self-calibration functions. Temperature compensation monitors environmental changes through built-in temperature sensors, automatically correcting temperature-drift measurement errors. Self-calibration periodically performs zero-point and span calibration, eliminating long-term drift. These technologies ensure reliable pressure data in complex laser environments, establishing foundations for precise pressure control.
2. Technical Requirements for Laser Machine Pressure Control Systems
Key Parameters for System Pressure Monitoring
Laser machines contain multiple precisely controlled pressure points including laser cavity pressure, auxiliary gas pressure, and cooling system pressure. Laser cavity pressure directly affects laser medium working states, requiring maintenance within specific ranges for stable power output. Auxiliary gas pressure relates to cutting and welding quality, with fluctuations causing uneven cuts or welding defects. Cooling system pressure affects laser heat dissipation, with insufficient pressure potentially triggering overheat protection. Absolute pressure sensors must simultaneously monitor these critical points, providing comprehensive pressure status information. Sensor measurement ranges typically cover 0-1MPa, meeting most laser machine monitoring requirements.
Safety Protection and Alarm Mechanisms
Laser machines as precision equipment have strict safety requirements. Absolute pressure sensors provide safety protection functions beyond pressure monitoring. When system pressure exceeds safety thresholds, sensors immediately trigger alarm signals, activating laser protection mechanisms. These mechanisms include laser power reduction, gas supply cutoff, and emergency shutdown, preventing pressure abnormalities from causing equipment damage or personnel injury. Sensor rapid response characteristics ensure timely abnormal pressure detection, providing sufficient reaction time for safety protection. Multi-level alarm settings allow systems to implement different protection measures based on pressure deviation degrees, ensuring safety while minimizing production impact.
Control Precision and Feedback Regulation
Laser machine processing quality largely depends on pressure control precision. Absolute pressure sensors provide real-time pressure feedback signals for laser control systems, enabling automatic parameter adjustment based on pressure changes. In cutting applications, sensors monitor auxiliary gas pressure while control systems adjust gas flow based on feedback signals, ensuring constant pressure during cutting. During welding, sensors monitor protective gas pressure, preventing oxidation affecting quality. This closed-loop control significantly improves laser processing accuracy and consistency. Sensor high precision and stability ensure control systems achieve Pa-level pressure control accuracy, meeting high-end laser processing requirements.
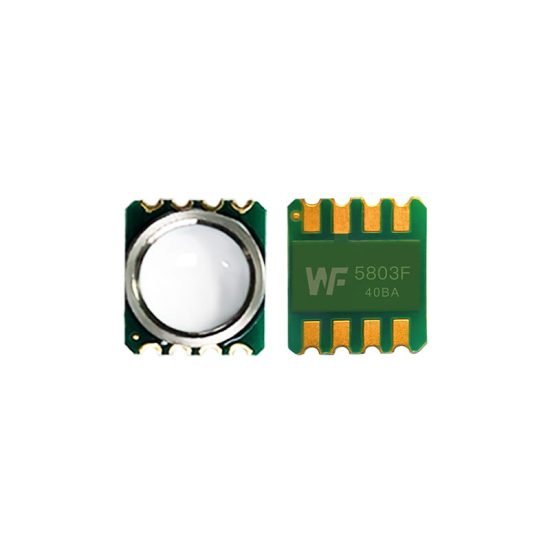
3. Sensor Integration and System Configuration
Installation Configuration and Interface Connection
Absolute pressure sensor installation positions in laser machines require comprehensive consideration of measurement accuracy, maintenance convenience, and system safety. Sensors typically install near laser heads on gas pipelines through threaded or flanged connections. Flush sensing surface design avoids creating vortices or dead zones in gas flow channels, reducing measurement errors and maintenance requirements.
Signal Processing and Data Transmission
Absolute pressure sensor output signals require conditioning and digitization for laser control system use. Modern sensors integrate high-precision ADCs and microprocessors for real-time pressure signal processing and correction. Signal processing includes temperature compensation, linearization correction, and digital filtering, ensuring output signal accuracy and stability. For data transmission, sensors support multiple communication protocols for compatibility with different laser controller brands. Advanced sensors feature network communication capabilities supporting Ethernet or wireless transmission for remote monitoring and data recording. This intelligent signal processing and transmission capability makes sensors important components of laser machine intelligent systems beyond simple measurement devices.
System Integration and Compatibility
Absolute pressure sensors require seamless integration with laser machine overall control systems, demanding good compatibility and flexible configuration capabilities. Sensors communicate with PLCs or embedded controllers through standard industrial protocols, achieving real-time pressure data transmission and processing. During system integration, sensor measurement range, accuracy class, and response time parameters must match specific laser application requirements. Sensor software configuration tools allow users to adjust measurement parameters, alarm thresholds, and output formats according to application needs. This flexible configuration capability enables single sensor models to adapt to different laser machine application requirements, reducing inventory costs and maintenance complexity. Good system integration capabilities ensure sensors fully utilize performance advantages, providing reliable pressure control support for laser machines.
4. Application Scenarios and Performance
Pressure Control in Laser Cutting Machines
Laser cutting machines have strict auxiliary gas pressure control requirements, with absolute pressure sensors playing core roles. Cutting different materials and thicknesses requires pressure adjustments, with sensors monitoring pressure changes real-time ensuring cutting process stability. Oxygen cutting typically controls pressure at 0.3-0.8MPa, while nitrogen cutting may reach 1.5MPa, requiring precise pressure measurement within these ranges. Pressure control accuracy directly affects cut surface quality, with high-precision absolute pressure sensors limiting control errors within ±1%, ensuring smooth cutting surfaces. Sensor rapid response characteristics enable systems to promptly address cutting process pressure fluctuations, maintaining cutting quality consistency. In high-speed cutting applications, millisecond sensor response times ensure real-time pressure control, meeting modern laser cutting machine efficiency and quality requirements.
Protective Gas Monitoring in Laser Welding Systems
Laser welding processes require protective gases preventing weld oxidation, with absolute pressure sensors monitoring protective gas pressure and flow. Inert gas pressures like argon or nitrogen require precise control – excessive pressure affects penetration depth while insufficient pressure fails to effectively protect welds. Sensors monitor gas pressure near welding heads, providing real-time feedback for control systems to automatically adjust gas flow valve openings. In precision welding applications, protective gas pressure control accuracy requirements reach ±0.5%, with absolute sensor high-precision characteristics fully meeting these requirements. Sensors also feature leak detection functions, promptly discovering and alerting protective gas system leaks, preventing welding quality impact. This intelligent monitoring and protection functionality significantly improves laser welding reliability and yield rates.
Gas Flow Pressure Management in Laser Marking Machines
Laser marking machines have relatively lower pressure control requirements but still need absolute pressure sensors ensuring gas flow pressure stability. Auxiliary gas flow during marking helps remove marking-generated smoke and heat, maintaining clean marking areas. Sensors monitor gas flow pressure ensuring marking effect consistency and clarity. In high-precision marking applications, minor gas flow pressure changes may affect marking depth and contour clarity, with absolute sensor precise monitoring providing marking quality assurance. Sensor maintenance-free characteristics particularly suit marking machines requiring long continuous operation, reducing maintenance downtime frequency. Universal characteristics enable sensors to adapt to different marking materials and process requirements, providing flexible pressure control solutions for laser marking machines.
5. Technical Advantages and Reliability Assurance
High-Precision Measurement and Long-Term Stability
Absolute pressure sensors employ advanced MEMS technology achieving high-precision measurement while realizing excellent long-term stability. Sensor measurement accuracy reaches 0.1% full scale with annual drift below 0.02%, ensuring laser machine pressure control accuracy during long-term use. Silicon-based MEMS structures feature good repeatability and reliability with strong overload resistance, withstanding 2-3 times range overpressure without damage. Temperature drift coefficients below 0.01%/°C maintain stable measurement performance within laser operating temperature ranges. These technical characteristics enable sensors to work reliably long-term in harsh industrial environments, providing continuous stable pressure control support for laser machines.
Rapid Response and Real-Time Control
Laser machine processing involves rapid pressure changes requiring absolute pressure sensors with fast response capabilities. Modern MEMS absolute pressure sensors typically feature 1-5 millisecond response times, promptly capturing pressure changes and providing real-time control system feedback. This rapid response characteristic proves particularly important for pressure-sensitive applications like laser cutting and welding. Built-in digital signal processors calculate pressure change rates and trends real-time, providing data support for predictive control. High sampling rates ensure no important pressure change information gets missed, providing technical assurance for precise pressure control. Rapid response combined with high-precision measurement enables laser machines to achieve true real-time pressure control, significantly improving processing quality and efficiency.
Environmental Adaptability and Durability Design
Laser machine operating environments are relatively harsh, featuring high temperatures, vibration, and electromagnetic interference, requiring absolute pressure sensors with good environmental adaptability. Sensor housings use stainless steel or special alloy materials providing good corrosion resistance and mechanical strength. Sealing ratings reach IP67, preventing dust and liquid intrusion. Anti-vibration design ensures normal sensor operation in mechanical vibration environments with vibration acceleration up to 50g. Electromagnetic compatibility design enables stable sensor operation in strong electromagnetic interference environments, unaffected by laser and drive circuit interference. Operating temperature ranges cover -40°C to +125°C, meeting various application environment requirements. These durability designs ensure sensor reliable operation throughout laser machine lifecycles, reducing replacement and maintenance costs.
บทสรุป
Absolute pressure sensors play irreplaceable important roles in laser machine pressure parameter precision control. Through advanced MEMS technology and multi-mode detection functions, these sensors provide high-precision, rapid-response pressure monitoring capabilities for laser machines. From cutting, welding to marking applications, absolute pressure sensors ensure precise pressure parameter control, directly improving laser machine processing quality and operational stability. Sensor high reliability, environmental adaptability, and maintenance-free characteristics make them indispensable core components of modern laser machines. As laser technology continues developing, absolute pressure sensors will continue playing key roles in enhancing laser machine performance, providing strong support for laser processing industry technological advancement.
บทนำข้างต้นเป็นเพียงรอยขีดข่วนพื้นผิวของการใช้งานของเทคโนโลยีเซ็นเซอร์ความดัน. เราจะสำรวจองค์ประกอบเซ็นเซอร์ประเภทต่าง ๆ ที่ใช้ในผลิตภัณฑ์ต่าง ๆ, พวกเขาทำงานอย่างไร, และข้อดีและข้อเสียของพวกเขา. หากคุณต้องการรายละเอียดเพิ่มเติมเกี่ยวกับสิ่งที่กล่าวถึงที่นี่, คุณสามารถตรวจสอบเนื้อหาที่เกี่ยวข้องในภายหลังในคู่มือนี้. หากคุณถูกกดเวลา, คุณสามารถคลิกที่นี่เพื่อดาวน์โหลดรายละเอียดของคู่มือนี้ ข้อมูลผลิตภัณฑ์เซ็นเซอร์ความดันอากาศ.
สำหรับข้อมูลเพิ่มเติมเกี่ยวกับเทคโนโลยีเซ็นเซอร์อื่น ๆ, โปรด เยี่ยมชมหน้าเซ็นเซอร์ของเรา.