Katalog
The scientific setting of sensor operating temperature ranges directly affects equipment performance stability and service life. This article systematically explains the core basis for sensor temperature range formulation from four dimensions: material properties, application environments, international standards, and reliability testing. Through in-depth analysis of practical application requirements for typical devices such as MEMS pressure sensors, it clarifies the differentiated requirements for temperature adaptability in different industries, providing practical standard reference frameworks for engineers and technical decision-makers.
1. Material Properties Determine Temperature Range Boundaries
Thermal Stability Analysis of Sensitive Element Materials
The materials used in sensor core sensitive elements directly determine their temperature tolerance limits. Silicon-based piezoresistive materials, as the main sensitive elements of MEMS pressure sensors, maintain stable crystal structures within the -55°C to +125°C range, beyond which irreversible performance degradation occurs. Metal thin-film strain gauges typically work in industrial environments from -40°C to +85°C, while ceramic piezoelectric materials can withstand wider temperature ranges, with some high-temperature ceramic materials operating above 200°C.
Temperature Adaptation Requirements for Packaging Materials
Packaging materials must not only protect internal sensitive units but also maintain structural integrity under extreme temperatures. Thermosetting epoxy resins are widely used in conventional industrial sensor packaging, with glass transition temperatures typically around 120°C. For high-temperature applications, high-performance materials like polyimide and polyphenylene sulfide become preferred choices, capable of withstanding sustained high temperatures above 150°C. In low-temperature environments, the material’s embrittlement temperature becomes a key consideration, ensuring packaging materials retain sufficient mechanical strength at minimum operating temperatures.
Temperature Compatibility of Circuit Components
Internal signal conditioning circuits, compensation circuits, and other electronic components within sensors also have temperature limitations. Commercial-grade integrated circuits typically operate from 0°C to +70°C, industrial-grade devices extend to -40°C to +85°C, while military-grade components can withstand extreme temperatures from -55°C to +125°C. These circuit component temperature characteristics often become limiting factors for entire sensor systems.
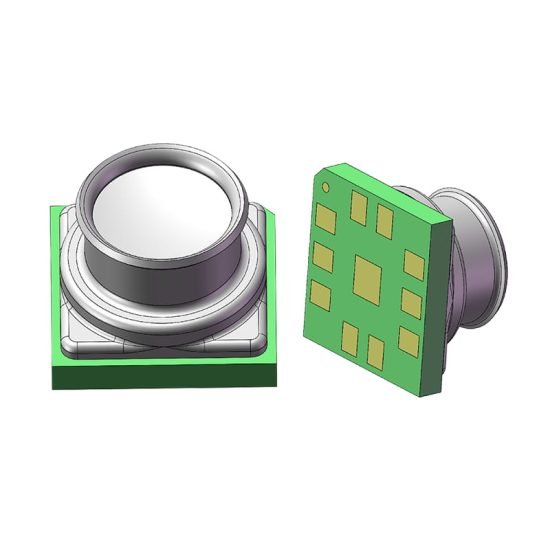
2. Application Environment's Differentiated Temperature Requirements
Industrial Automation Temperature Requirements
In industrial automation environments, sensors face relatively controllable temperature challenges. General production line environments range from -20°C to +70°C, but special processes like high-temperature smelting and glass manufacturing can reach hundreds of degrees locally. Remote installation or thermal isolation techniques are needed, placing sensor bodies in relatively moderate environments. For cold storage and cold chain logistics applications, sensors must ensure normal operation below -40°C.
Automotive Electronics' Extreme Temperature Challenges
Automotive environments present the most dramatic temperature variations in sensor applications. Engine compartment MAP sensors, EGR differential pressure sensors, and others must withstand -40°C to +125°C or higher temperature ranges. Tire Pressure Monitoring System (TPMS) sensors must adapt to seasonal temperature changes while withstanding local high temperatures from tire friction during high-speed driving. Modern automotive sensor designs typically follow AEC-Q100 and AEC-Q103 standards, ensuring reliability under various global climate conditions.
Aerospace Applications' Extreme Temperature Tests
Aerospace applications impose the most stringent temperature adaptability requirements on sensors. High-altitude environments can reach -70°C, while engine vicinity temperatures can exceed 200°C. Satellite payload sensors must also withstand extreme temperature cycles in space environments, instantly jumping from +120°C in sunlit areas to -180°C in shadow zones. Such applications typically require specialized temperature compensation techniques and special material processes.
3. International Standards' Technical Specification Guidance
IEC 60068 Environmental Test Standards Series
The International Electrotechnical Commission IEC 60068 series provides authoritative guidance for sensor temperature testing. IEC 60068-2-1 specifies standard procedures for low-temperature testing, including pretreatment, test condition setting, and performance evaluation. IEC 60068-2-2 corresponds to high-temperature test specifications, while IEC 60068-2-14 specifically addresses temperature cycling tests. These standards not only specify test methods but also clarify temperature range requirements for different application grades.
Military Standard MIL-STD-810's Strict Requirements
MIL-STD-810 military standards represent the highest level of sensor environmental adaptability. Methods 501.7 och 502.7 correspond to high-temperature and low-temperature testing respectively, with standard operating temperature ranges from -55°C to +125°C and storage temperature ranges extending to -65°C to +150°C. The standard also specifies detailed parameters including temperature change rates, holding times, and cycle numbers, ensuring military sensor reliability under various extreme environments.
Automotive Industry's Specialized Standards
The automotive electronics field has formed a standard system centered on AEC-Q100 and AEC-Q103. AEC-Q100 defines temperature grades for automotive integrated circuits, from Grade 0’s -40°C to +150°C to Grade 3’s -40°C to +85°C. AEC-Q103 specifically targets MEMS devices, adding considerations for automotive-specific environmental factors like mechanical shock and vibration. These standards provide clear technical basis for automotive sensor temperature range setting.
4. Reliability Testing Verification Technical Requirements
Temperature Cycling Test Design Principles
Temperature cycling tests are core methods for verifying sensor temperature adaptability. Tests typically set cycling ranges from -40°C to +85°C, with each cycle including heating, high-temperature hold, cooling, and low-temperature hold phases. Cycle numbers are determined by application requirements: generally 100-500 cycles for consumer products, 1000-5000 cycles for industrial products, and over 10,000 cycles for military applications. Sensor output characteristics must be continuously monitored during testing to evaluate performance stability.
Thermal Shock Test Extreme Evaluations
Thermal shock tests simulate sensor performance under rapid temperature changes. Test equipment has rapid temperature switching capabilities, typically completing temperature jumps from -40°C to +125°C within 30 seconds. This extreme testing can reveal potential issues like packaging stress, solder joint fatigue, and material mismatch. Through thermal shock testing, sensor reliability boundaries can be determined when facing sudden temperature changes in actual applications.
Long-term Stability Verification Methods
Long-term high-temperature aging tests are important means for evaluating the reasonableness of sensor temperature range settings. Sensors are placed in environments close to their temperature limits, typically 85°C to 105°C, for 1000 to 8760 timmar. Key parameters like zero drift, sensitivity changes, and linearity are regularly checked during testing. Through accelerated aging tests, sensor performance change trends over actual service life can be predicted.
5. Engineering Practice Principles for Temperature Range Setting
Reasonable Safety Margin Allocation
In engineering practice, sensor temperature range setting requires consideration of safety margins. Generally, it’s recommended to reserve 5°C to 10°C temperature buffer zones based on application requirements. This design redundancy can handle unexpected field environment fluctuations, performance drift from long-term aging, and device variations during mass production. Reasonable safety margins ensure system reliability while avoiding cost increases from over-design.
Differentiated Management of Operating and Storage Temperatures
Sensor operating and storage temperatures must be strictly differentiated. Operating temperature refers to environmental temperature ranges when sensors are powered and normally outputting signals, while storage temperature is the temperature limit without permanent damage in non-operating states. Storage temperature ranges are typically 10°C to 20°C wider than operating temperature ranges, ensuring product safety during transportation and storage.
Special Considerations for Local Heat Sources
In actual applications, sensors may face instantaneous effects from local heat sources. Till exempel, thermal radiation from engine startup moments or temperature mutations from industrial equipment switching operations. These short-term, localized temperature exceedances may not affect overall environmental temperature but could damage sensors. Därför, temperature range setting must consider these special conditions and implement appropriate protective measures.
Slutsats
Scientific setting of sensor operating temperature ranges is a comprehensive technical decision process involving material science, application engineering, standard specifications, and reliability testing. From basic material property limitations to actual application environment requirements, from international standard technical guidance to reliability testing verification requirements, each link significantly impacts final temperature range settings. As electronic systems expand into more extreme environments, sensor temperature adaptability requirements will become increasingly stringent. Engineers and technical decision-makers should comprehensively consider technical feasibility, cost-effectiveness, and reliability requirements based on specific application scenarios to formulate temperature range standards that both meet performance needs and possess engineering feasibility.
Ovanstående introduktion repor bara ytan på tillämpningarna av trycksensorteknologi. Vi kommer att fortsätta utforska de olika typerna av sensorelement som används i olika produkter, Hur de arbetar, och deras fördelar och nackdelar. Om du vill ha mer detaljer om vad som diskuteras här, Du kan kolla in det relaterade innehållet senare i den här guiden. Om du är pressad i tid, Du kan också klicka här för att ladda ner detaljerna i dessa guider Lufttryckssensor Produkt PDF -data.
För mer information om andra sensorteknologier, behaga Besök vår Sensors -sida.