Accurate measurement of liquid flow, one of the core requirements of many industrial processes, relies on the technical support of flow sensors. So how exactly do flow sensors help us achieve accurate liquid flow measurement? Today we’ll talk about this topic and take you through the technical principles behind flow sensors to help you make more informed decisions when choosing the right equipment.
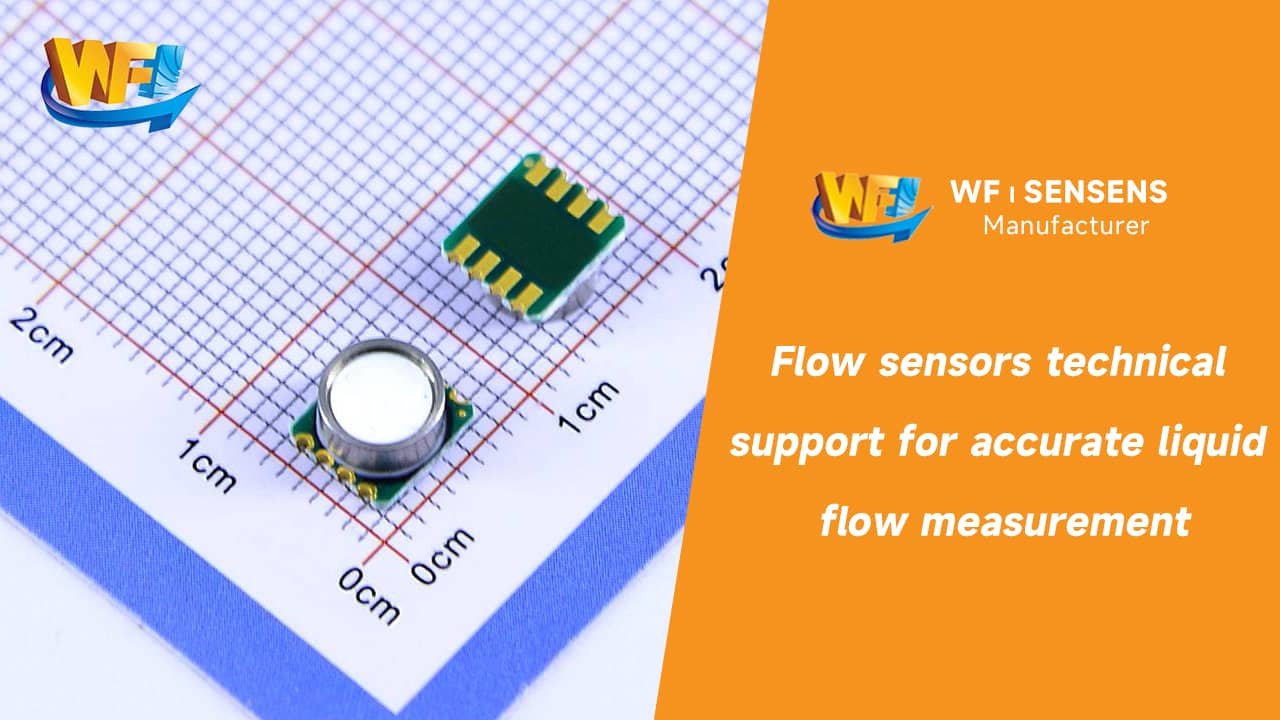
Каталог
Let’s start understanding!
How do flow sensors actually work?
Flow sensors, as the name suggests, are used to measure the speed and volume of liquid (or even gas) flow. How they work involves a variety of technologies, commonly including:
1. Differential pressure flow sensors
This type of sensor calculates the flow rate by measuring the change in pressure caused by the flow of fluid. As a fluid flows through a pipe, differences in flow rates cause the fluid to create a pressure difference at different locations. By accurately measuring this pressure difference, the sensor is able to invert the flow rate of the fluid. This approach is suitable for applications with high flow rates or large volume flows, such as flow monitoring in petroleum pipelines.
2. Vortex flow sensors
Vortex flow sensors measure flow by detecting the frequency of vortices created by fluid flow. When a fluid passes through a disturbing fluid, periodic vortices are created downstream. The sensor uses the frequency of these vortices to derive the flow rate. Vortex flow sensors are well suited for a wide range of fluids, including corrosive fluids.
3. Electromagnetic Flow Sensors
Electromagnetic flow sensors are based on Faraday’s law of electromagnetic induction. When a liquid flows through a sensor pipe with a magnetic field, the motion of the liquid creates a voltage on both sides of the pipe. Based on this voltage, the sensor calculates the flow rate of the liquid. This type of flow sensor is suitable for liquids with high conductivity and is especially common in the water treatment and chemical industries.
4. Ultrasonic flow sensors
Ultrasonic flow sensors measure the liquid flow rate by transmitting and receiving ultrasonic signals. The sensors utilize the effect of the liquid flow on the acoustic waves (e.g., delay time or frequency change) to measure the flow rate. They have low requirements for the nature of the liquid, are suitable for a wide range of liquids and gases, and do not require direct contact with the fluid.
How to ensure accurate measurement of liquid flow?
Although there are various types of flow sensors, there are a few technical points behind them that cannot be ignored if you want to measure liquid flow accurately:
1. Highly accurate sensor elements
Accurate flow measurement relies on high-precision sensor elements. На пример, the use of advanced pressure sensors, thermal elements or high-quality electronic components ensures that flow readings are not affected by external disturbances and errors. High accuracy means that very small changes in flow rate can be accurately captured, avoiding the accumulation of errors.
2. Temperature and pressure compensation
Liquid flow is often affected by changes in temperature and pressure, so modern flow sensors often incorporate temperature and pressure compensation. By monitoring and correcting for the effects of these variables on the measurement results in real time, the sensor is able to maintain highly accurate measurements under varying operating conditions.
3. Signal processing and data calibration
Accurate liquid flow measurement is not only the work of the sensor itself, but is also dependent on efficient signal processing technology. By means of digital signal processing algorithms, flow sensors are able to convert raw signals into precise flow data. Modern sensors also perform data calibration and filtering to effectively reduce noise and improve measurement stability.
4. Field adjustability and remote monitoring
Many modern flow sensors support on-site adjustment of parameters or real-time adjustments via remote monitoring systems. This is particularly important for industrial applications, as they are often required to operate under different operating conditions. Users can adjust sensor settings based on real-time data to ensure that flow measurements are always accurate.
Practical applications of flow sensors: in which industries can they be found?
✅ Water treatment industry
Flow sensors are widely used in water and wastewater treatment plants. They are used to monitor the flow of water to ensure that it remains within a predetermined range to optimize the treatment process and ensure efficient use of resources.
✅ Chemical and petroleum industries
In chemical production and oil transportation pipelines, flow sensors are an important tool to ensure accurate metering of liquids (e.g. oil, chemicals, итд.). Especially in high-temperature, high-pressure, highly corrosive environments, accurate flow monitoring helps ensure production safety and process stability.
✅ Food and beverage industry
In the food processing and beverage manufacturing process, accurate liquid flow measurement is critical to ensure product quality, taste and recipe consistency. Flow sensors can help manufacturers accurately control liquid ingredients to improve productivity and product consistency.
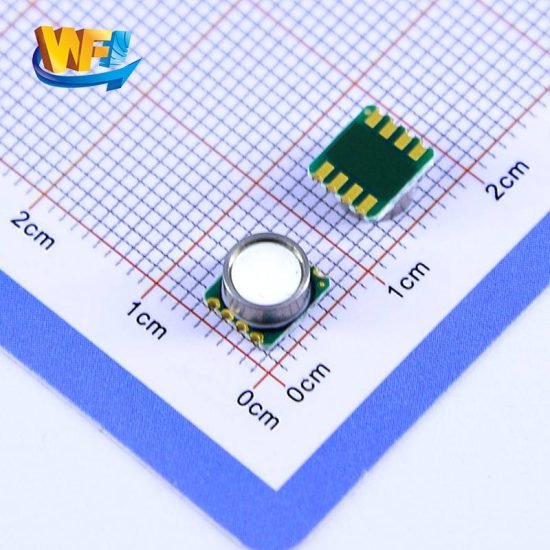
How to choose the right flow sensor: practical advice
- Choosing the right flow sensor not only improves the performance of your system, but also avoids inaccurate measurements or equipment failures due to wrong choices. Here is some practical advice to help you make the right choice for different needs.
1. Determine the type of liquid
First, it is important to identify what type of fluid your flow sensor will be used to measure. Different fluids (e.g., water, oil, chemicals, food, итд.) have different requirements for sensors. На пример:
- Liquids with high conductivity: If you are measuring water or other liquids with high conductivity, electromagnetic flow sensors will be a good choice because they do not rely on the physical properties of the fluid, only that the liquid has a certain degree of conductivity.
- Corrosive liquids: For corrosive liquids (such as acid and alkali solutions), vortex flow sensors or turbine flow sensors are often encapsulated with corrosion-resistant materials that can provide long-term stable performance.
- Oil or non-conductive liquids: If the liquid is oil or other non-conductive liquids, turbine flow meters or ultrasonic flow sensors are the more ideal choice.
2. flow range
- Low flow applications: If the application scenario involves lower flow rates, such as metering trace amounts of fluid, it is recommended to choose a high sensitivity sensor, such as a thermal flow sensor or some types of vortex flow sensors.
- High flow applications: For industrial scenarios with high flow rates, such as oil pipelines or water treatment, differential pressure flow sensors, turbine flow meters or electromagnetic flow meters usually perform better.
3. Accuracy and repeatability
- High accuracy requirements: If the application scenario requires high accuracy, such as precision chemical or pharmaceutical industries, you should choose flow sensors with high accuracy and low error range, such as electromagnetic flow sensors or ultrasonic flow sensors.
- Repeatability: High repeatability is important for day-to-day measurements. Ensure that the selected sensor can maintain consistent performance after a long period of use.
4. Operating environmental conditions
- Температурни опсег: Different types of flow sensors can withstand different temperature ranges. If working in extreme temperatures, choose a sensor that is capable of stable operation at high or low temperatures, such as a vortex flow sensor, which can cope with a wide range of temperatures.
- Pressure requirements: If the application involves a high pressure environment (e.g. oil pipelines), choose a sensor that is resistant to high pressure, such as a differential pressure flow sensor.
5. Mounting requirements
- Pipe size and shape: Select the appropriate sensor according to the diameter and shape of the pipe. Some flow sensors require sufficient diameter in the pipe to function properly, while others can be adapted to small or non-standard pipes.
- Fluid Flow Direction: Ensure that the selected sensor is appropriate for the current fluid flow direction. Some sensors may require special settings if reverse flow monitoring is required.
6. Budget and cost-effectiveness
- Long-term investment: If reliable operation over a long period of time is required, choosing a higher quality sensor may be a higher initial investment, but in the long run, it can effectively reduce maintenance and replacement costs.
- Low-budget applications: For applications with a limited budget, it may be possible to choose a lower-cost sensor (e.g., a turbine flowmeter), but there is a trade-off between accuracy and stability.
7. Maintenance and calibration requirements
- Maintenance frequency: Some flow sensors may require periodic cleaning, calibration, or component replacement. Selecting sensors with low maintenance requirements can reduce long-term O&M costs.
- Technical support: Ensure that the flow sensor you choose offers reliable technical support and service in the event of a malfunction.
Закључак: Accurate measurement, reliable support
Flow sensors provide powerful technical support in liquid flow measurement. Different types of sensors utilize their own unique operating principles and technologies depending on the requirements of the specific application. High-precision sensor elements, temperature and pressure compensation, signal processing technology and remote monitoring functions all provide a guarantee of accurate liquid flow measurement. Whether in the water treatment, chemical, petroleum, or food industries, flow sensors play a vital role.
Select the right flow sensor and understanding how they work will help you achieve accurate and reliable liquid flow measurement in a variety of applications.
Горњи увод огреботине само површину апликација технологије сензора притиска. И даље ћемо истражити различите врсте сензорских елемената који се користе у различитим производима, Како раде, и њихове предности и недостатке. Ако желите више детаља о томе о чему се овде расправља, Касније можете да проверите повезани садржај у овом водичу. Ако сте притиснути време, Овде можете да кликнете и да преузмете детаље ових водича Подаци о сензору притиска ваздуха ПДФ.
За више информација о другим сензорским технологијама, молимо вас Посетите нашу страницу сензора.