Pressure sensors can be used to directly convert the measured pressure into various forms of telecommunication signals to meet the requirements of centralized detection and control of automation systems, and are therefore widely used in industrial production.
Pressure sensors are used extensively in many monitoring and control applications. In addition to direct pressure measurement, pressure sensors can also be used to indirectly measure other quantities such as liquid/gas flow, velocity, water surface height or altitude.
There is also a class of pressure sensors designed to measure water pressure, depth, and air pressure. Example applications are the monitoring of air pressure in altimeters or the pressure of gases in inflatable pumps. Such sensors are generally manufactured from silicon materials, such as wafers.

Содржина
Some pressure sensors, such as those used in traffic-enforcement cameras, operate in a binary mode, Т.е., when the pressure reaches a certain value, the sensor controls the switching on or off of the circuit, and these types of pressure sensors are also known as pressure switches.
A pressure sensor is a device or equipment that senses pressure signals and converts them into usable output signals according to certain rules.
Pressure sensors usually consist of a pressure sensitive element and a signal processing unit. Depending on the type of pressure being tested, pressure sensors can be categorized as gauge pressure sensors, differential pressure sensors, and absolute pressure sensors.
Pressure sensors are one of the most commonly used sensors in industrial practice, and are widely used in various industrial automation environments, involving water conservancy and hydropower, railway and transportation, intelligent construction, production automation, petrochemical, oil well, power, ship, machine tools, pipelines and many other industries.
Application of Pressure Sensor in Fresh Air System
Pressure sensors measure the pressure difference between the two ends of the duct as a measure of volumetric flow rate. The sensor is installed in the bypass channel of the main flow line. In volumetric flow controllers for variable air volume (VAV) systems, pressure measurements are used to control the position of dampers in the closed-loop control circuit, making on-demand fresh air control possible.
Pressure sensors are an important component of such systems and play a key role in quality control.
The switching on and off of dampers for ventilation control in a single room results in pressure changes in the ventilation ducts. On-demand fresh air control is achieved by controlling the fans in the ventilation system to ensure that the pressure in the ducts remains constant at all times, thus providing effective ventilation and ensuring proper air conditioning operation. Pressure sensors monitor the inlet pressure for fan power control. In this way, the pressure sensor contributes significantly to the safe and energy-efficient operation of the ventilation system.
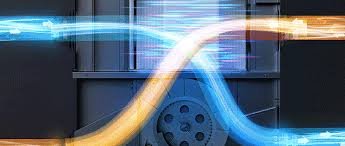
In an air-conditioned room, air should be supplied and extracted in such a way as to minimize pressure differences between zones or between a single zone and its surroundings. On the other hand, a constant positive pressure difference must be ensured in clean rooms to prevent the entry of untreated air.
Constant negative pressure differences in laboratories and hospitals prevent the spread of germs and harmful substances. In all of these applications, high-precision pressure sensors ensure the safety and comfort of the environment by monitoring small pressure differences.
Pressure Sensors in Weighing Systems
Pressure sensing technology is increasingly being utilized in commercial weighing systems for industrial control.
In many control processes, it is often necessary to collect pressure signals and convert them into telecommunication signals capable of automated control. This type of pressure control device made with pressure sensors as the core component is generally referred to as an electronic weighing system, and is playing an increasingly important role in modern production as an online control tool for the flow of materials in various industrial processes.
In the process automation of weighing, pressure sensors are required not only to sense gravity signals, but also to be reliable, dynamically responsive, and resistant to interference.
By integrating the pressure sensor with the measurement circuit, the signal provided by the pressure sensor can be processed by the detection system to be directly displayed, recorded, printed, and stored for feedback regulation and control, thus further increasing the degree of automation and control of the weighing process.
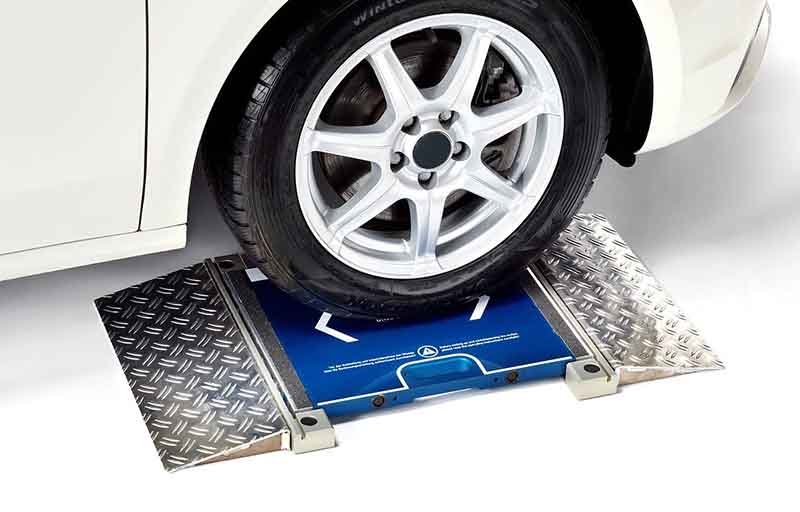
Pressure Sensors for Water Treatment Applications
The environmental water treatment industry has seen rapid growth in recent years and has a promising future. In the water supply and wastewater treatment process depends on the use of pressure sensors for system protection and quality assurance to provide an important means of control and monitoring.
Water treatment mainly includes water level monitoring of rivers and dams, sewage treatment and drinking water treatment, constant pressure water supply systems and other oriented. According to the different ways of sensor installation, can be divided into built-in type and external type. The built-in type mainly uses liquid level transmitters, and the external type mainly uses industrial pressure sensors.
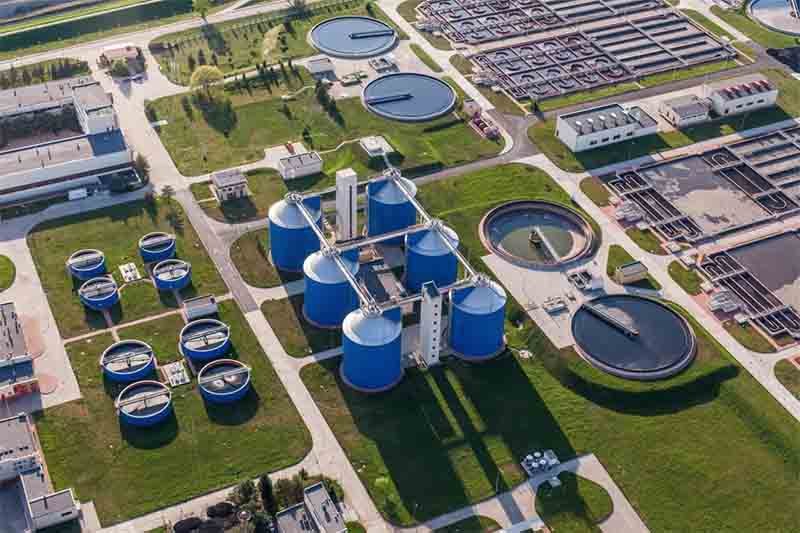
Pressure Sensors in the Medical Industry
Pressure sensors play an important role in medical history taking and minimally invasive surgery monitoring. Arterial blood pressure, intracranial pressure, and intrapulmonary pressure are all important parameters in the medical process. Покрај тоа, monitoring, treatment, and health care are all dependent on the precise measurement of pressure sensors.
In addition to sophisticated medical and surgical facilities, medical devices such as electronic blood pressure monitors, which are commonly used in daily life, also use pressure sensors to realize autonomous and real-time measurements.
With the development of modern medical technology, the pressure sensors used in the medical industry have higher requirements in terms of accuracy, reliability, стабилност, volume, итн., which also promotes the vigorous development of medical pressure sensors.
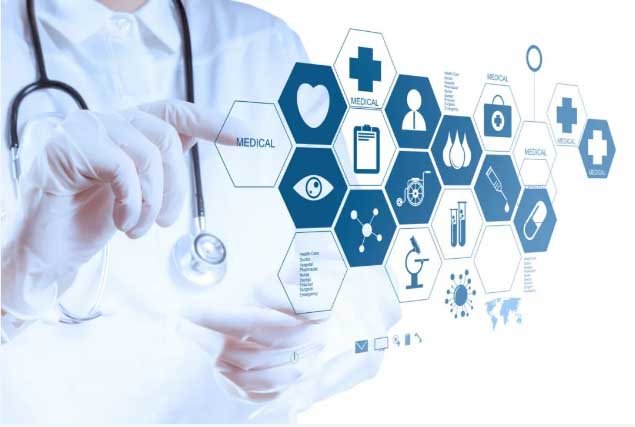
Pressure Sensors in Hydraulic Systems
Pressure sensors are used in hydraulic systems to accomplish closed-loop control of forces. When a control spool moves suddenly, a pressure spike of several times the operating pressure of the system is created in a very short period of time.
In typical mobile machinery and industrial hydraulics, any pressure sensor will quickly be destroyed if it is not designed for such extreme conditions.
The need to use shock-resistant pressure sensors, pressure sensors to achieve shock resistance there are 2 main methods, one is to change the strain gauge chip, the other method is an external coil, generally in the hydraulic system, the first method, mainly because of the ease of installation.
Another reason is that the pressure sensor also has to withstand the uninterrupted pressure pulsations from the hydraulic pump.
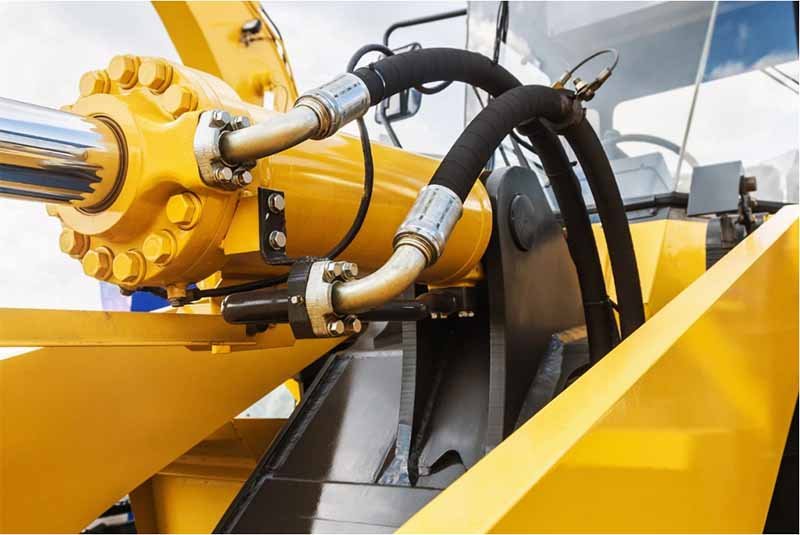
Pressure sensors for safety control systems
Pressure sensors are often used in safety control systems, mainly in the area of safety management systems for air compressors themselves. There are many sensor applications in the field of safety control, and it is not surprising that pressure sensors, as a very common type of sensor, are used in safety control systems.
In the field of safety control applications generally from the performance aspect to consider, from the price consideration, as well as from the actual operation of the safety and convenience to consider, the actual proof of the choice of pressure sensors is very good.
Pressure sensors use mechanical equipment processing technology to install some components and signal regulators and other devices on a very small chip. Small size is one of its advantages, and cheapness is another. To a certain extent, it can improve the accuracy of system testing.
In the safety control system, the pressure brought by the compressor is controlled to a certain extent by installing pressure sensors in the piping equipment of the outlet, which is considered as a certain protection measure and a very effective control system. When the compressor is started normally, if the pressure value does not reach the upper limit, then the controller will open the air inlet and adjust it to maximize the power of the equipment.
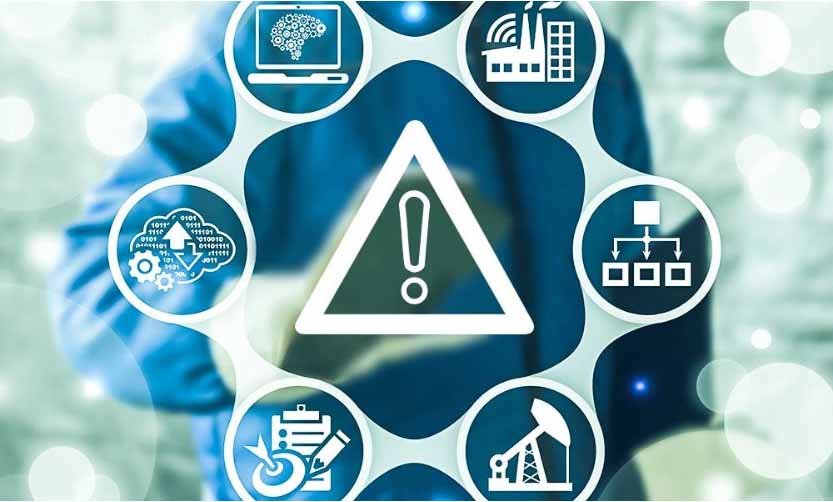
Pressure Sensors for Injection Molds
Pressure sensors play an important role in injection molding. Pressure sensors can be installed in the nozzle of the injection molding machine, in the hot runner system, in the cold runner system, and in the cavity of the mold. They measure the pressure of the plastic from the nozzle of the injection molding machine to the cavity of the mold somewhere during the injection, filling, holding and cooling processes.
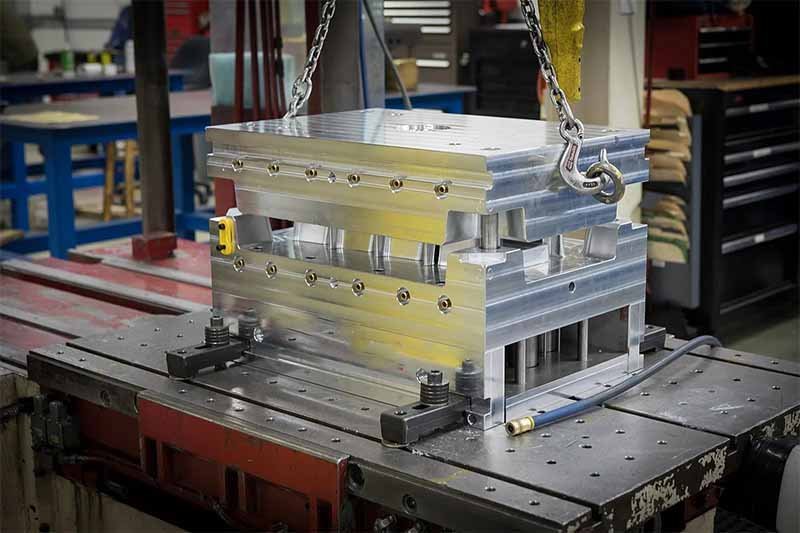
Pressure sensors used to monitor pressure in mines
There are many kinds of pressure sensors, and based on the special environment of mining pressure monitoring, mining pressure sensors mainly include: semiconductor piezoresistive pressure sensors, metal strain gauge pressure sensors, differential transformer pressure sensors, итн. These sensors are widely used in the mining industry. These sensors have a wide range of applications in the mining industry, and the specific type of sensor to be used should be selected according to the specific mining environment.
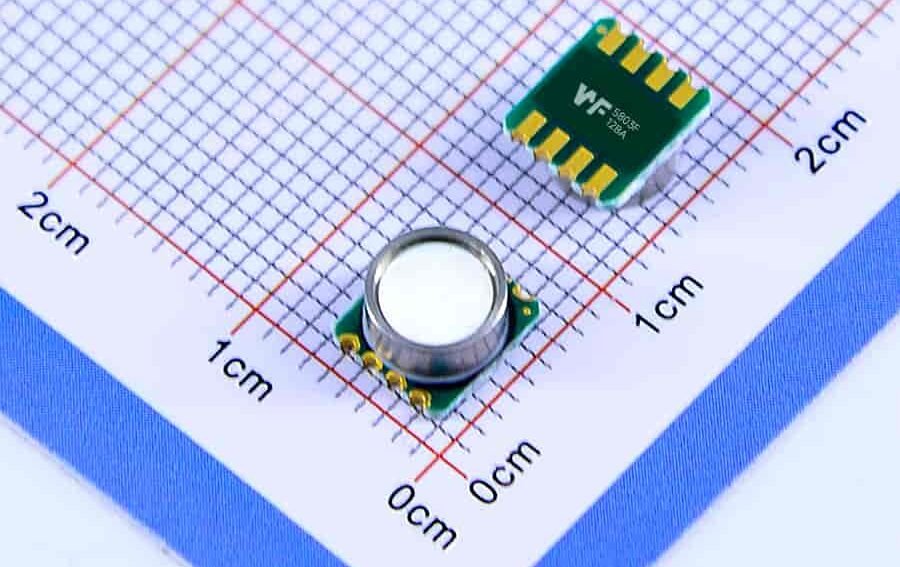
Pressure Sensors for Compressors, Air Conditioning and Refrigeration Equipment
Сензори за притисок are commonly used in air compressors and air-conditioning refrigeration equipment. These sensors are compact, easy to install, and the pilot ports are generally of a specialized valve pin design.
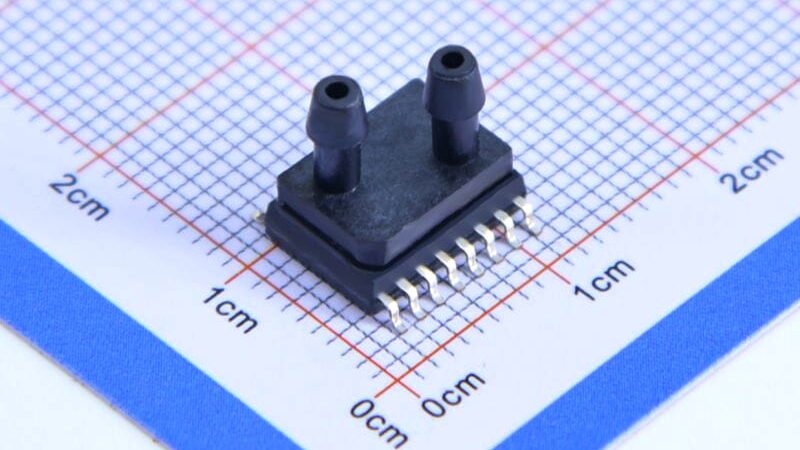