목록
일반적인 압력 센서 문제를 해결하는 방법
압력 센서는 많은 산업 및 상업용 응용 분야에서 필수 구성 요소입니다., 다양한 프로세스 제어 및 모니터링에 중요한 실시간 압력 측정 제공. 하지만, 기계 장치와 마찬가지로, 압력 센서는 때때로 실패 할 수 있습니다. 이 기사에서, 일반적인 압력 센서 문제를 해결하는 방법에 대한 안내서를 제공합니다., WF 압력 센서 및 기타 센서를 진단하고 수리하는 방법 포함.
출력 또는 불안정한 출력이 없습니다
압력 변환기가 출력이 없거나 잘못된 출력이있는 경우, 트랜스 듀서의 전기 연결 또는 트랜스 듀서 자체에 문제가있을 수 있습니다.. 연결이 올바른지 확인하고 멀티 미터 또는 공기압 센서 모듈로 센서 출력 전압을 테스트하려면 핀을 확인하십시오.. 전압이 지정된 범위 내에있는 경우, 문제는 센서 자체에 문제가있을 수 있습니다. 이 경우, 지원은 WFSensors 기술 지원에 문의하십시오.
제로 출력
압력 트랜스 듀서가 출력되는 경우 0., 트랜스 듀서의 전기 연결에 문제가있을 수 있습니다., 트랜스 듀서의 공급 전압, 또는 트랜스 듀서의 내부 전자 제품. 배선 핀아웃 다이어그램 및 공급 전압을 확인하여 지정된 범위 내에서 올바르게 연결되어 있는지 확인하십시오.. 핀이 납땜되고 전압이 올바른 경우, 문제는 센서의 내부 전자 제품에 문제가있을 수 있습니다. 이 경우, 지원을 위해 Factory 지원에 문의하십시오.
범위 외 출력
압력 트랜스 듀서의 측정 출력이 압력 범위를 벗어난 경우, 과도한 압력 때문일 수 있습니다, 결함이있는 트랜스 듀서, 또는 트랜스 듀서의 교정에 문제가 있습니다. 압력을 확인하여 센서의 정격 범위 내에 있는지 확인하십시오.. 압력이 지정된 범위 내에있는 경우, 센서 또는 교정에 문제가있을 수 있습니다.. 이 경우, 공장은 새로운 공기압 센서를 위해 연락 할 수 있습니다..

주목:연결 정의는 SOP 및 DIP 패키지 제품에 대해 동일합니다.
느리거나 지연된 응답
압력 트랜스 듀서에 응답이 느리거나 지연되는 경우, 트랜스 듀서의 전자 장치에 문제가 발생했을 수 있습니다., 배선, 또는 교정. 배선 연결이 올바르하고 부식이 없는지 확인하십시오.. 센서의 교정을 확인하여 지정된 한계 내에 있는지 확인하십시오.. 납땜 된 핀 연결 및 교정이 올바른 경우, 문제는 센서의 내부 전자 제품에 문제가있을 수 있습니다.
온도 드리프트
압력 변환기가 온도 드리프트가 발생하는 경우, 트랜스 듀서의 보상 회로에 문제가 있거나 트랜스 듀서의 교정으로 인한 것일 수 있습니다.. 연결이 정확하고 부식이 없는지 핀 배선을 확인하십시오.. 센서의 교정을 확인하여 지정된 범위 내에 있는지 확인하십시오.. 배선 및 교정이 올바른 경우, 문제는 센서의 보상 회로와 관련이있을 수 있습니다.
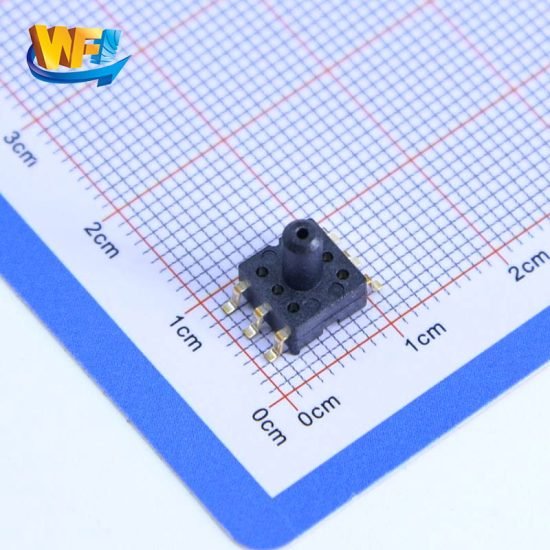
압력 센서가 실패하는 이유?
환경 적 요인
가혹한 환경은 센서 성능에 크게 영향을 줄 수 있습니다. 극한 온도에 노출, 습기, 부식성 물질, 진동은 마모를 가속화 할 수 있습니다. 적절한 인클로저와 코팅으로 센서를 보호하는 것이 필수적입니다..
전기 오버 스트레스
전기 오버 스트레스, 전압 스파이크 또는 정전기 방전과 같은 (ESD), 센서의 내부 전자 장치를 손상시킬 수 있습니다. 적절한 접지, 서지 보호, 신중한 취급은 이러한 문제를 방지 할 수 있습니다.
오염
오염 물질의 존재, 먼지와 같은, 기름, 또는 화학 물질, 센서의 압력 포트를 막거나 내부 부품을 부식시킬 수 있습니다.. 정기적 인 청소와 필터 사용은 오염 관련 장애를 방지 할 수 있습니다..
일반적인 압력 센서 문제를 해결하는 방법
초기 점검
육안 검사: 눈에 보이는 손상을 확인하십시오, 균열과 같은, 부식, 또는 느슨한 연결.
배선: 센서의 데이터 시트에 따라 모든 배선 연결이 안전하고 올바르게 연결되어 있는지 확인하십시오..
전원 공급 장치: 센서가 올바른 공급 전압을 받고 있는지 확인하십시오.. 자주, 전압이 부적절합니다.
압력 점검
알려진 압력을 적용하십시오: 교정 압력 소스를 사용하여 센서에 알려진 압력을 적용하십시오..
읽기를 비교하십시오: 센서의 출력을 예상 값과 비교하십시오. 중요한 편차는 문제를 나타냅니다.
누출을 확인하십시오: 센서의 판독 값에 영향을 줄 수있는 압력 라인이나 피팅에 누출이 없도록.
- 신호 컨디셔닝: 신호 컨디셔닝 회로에서 모든 문제가 있는지 확인하십시오, 결함이있는 OP-AMPS 또는 저항과 같은.
결론
위의 소개는 압력 센서 기술의 적용 표면 만 긁는 것만. 다양한 제품에 사용되는 다양한 유형의 센서 요소를 계속 탐색 할 것입니다., 그들이 어떻게 일하는지, 그리고 그들의 장점과 단점. 여기에서 논의 된 내용에 대한 자세한 내용을 원한다면, 이 안내서의 뒷부분에서 관련 콘텐츠를 확인할 수 있습니다.. 시간이 걸리면, 이 가이드의 세부 사항을 다운로드하려면 여기를 클릭하십시오. 공기 압력 센서 제품 PDF 데이터.
다른 센서 기술에 대한 자세한 내용, 제발 센서 페이지를 방문하십시오.