목록
1. Corrosive Environments and Application Background
1.1 Impact of Corrosive Media
공기 압력 센서는 자동차 시스템에서 의료 기기에 이르기까지 수많은 산업에서 중요한 역할을합니다.. 이 센서가 매일 안정적이고 정확한 판독 값을 제공하는 경우, 효율적인 운영과 임계 오류의 모든 차이를 만듭니다.. 이 기사에서, 우리는 탐구합니다 공기 압력 센서 안정성 상세히.
1.2 Real-World Application Examples
From industrial control systems to automotive safety measures and personal wearables, the demand for sensors that maintain high precision in aggressive environments is growing. 이 응용 프로그램에서, sensors must not only measure pressure and temperature reliably but also resist the damaging effects of corrosive agents.
2. Overview of MEMS Sensor Technology
2.1 Key Features of MEMS Design
MEMS technology enables the miniaturization and high integration of sensor components. 일반적으로, the sensor incorporates a silicon diaphragm with strain gauges placed along its edge. When subjected to pressure, the diaphragm deflects similarly to a trampoline, causing a change in the strain gauge resistance that can be measured.
2.2 Signal Conditioning and Digital Conversion
Within the sensor, integrated CMOS ASIC circuits compensate for temperature drift and other errors. The conditioned analog signal is then amplified, digitized, and transmitted via standard I2C or SPI interfaces, ensuring precise and reliable communication with a microprocessor.

3. Applications in Corrosive Environments
3.1 Industrial and Automotive Sectors
In industries like manufacturing and automotive safety systems, sensors are often used in environments that include corrosive gases or liquids. Besides delivering accurate measurements, these sensors must resist chemical damage over time. 예를 들어, certain volatile halogenated compounds from organic polymers can cause irreversible changes on MEMS surfaces.
3.2 Wearable Devices in Harsh Conditions
In the realm of sports watches and diving instruments, sensors must operate in chlorine-rich water. Advanced packaging techniques prevent corrosive substances from infiltrating sensitive sensor components, ensuring long-term, stable performance.
4. Operating Principles of MEMS Pressure Sensors
4.1 Strain Gauge Mechanism and Mechanical Response
When external pressure is applied, the silicon diaphragm deforms, and strain gauges located along its periphery alter their resistance. By employing a Wheatstone bridge configuration, the sensor boosts signal strength and minimizes noise, delivering a clean baseline for further processing.
4.2 Signal Offsets and Corrosion Effects
이상적으로, the differential output voltage should read 0V when no pressure is applied. Any offset typically signals that corrosion-induced changes in the sensor elements are at play, necessitating design considerations to maintain reliability.
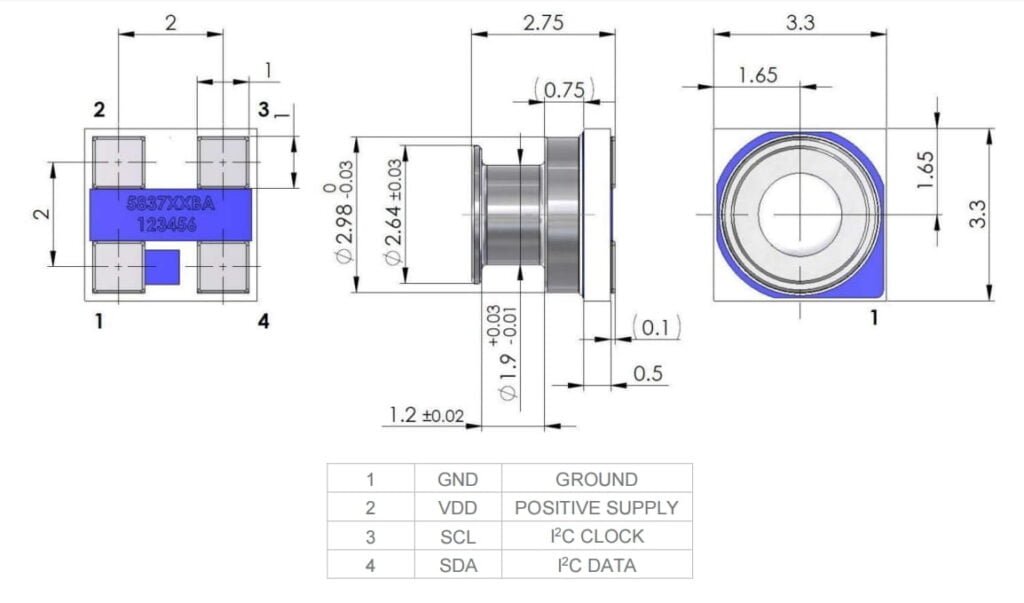
5. Packaging Strategies and Environmental Protection
5.1 The Role of Robust Packaging
Effective packaging ensures that the sensor is both in contact with the medium it monitors and adequately isolated from harmful substances. In harsh settings, the design must integrate compact yet robust connections to protect sensitive components against corrosive chemicals.
5.2 Material Selection and Assembly Techniques
To counteract attacks from aggressive oxidizers (such as fluorine, chlorine, bromine, and iodine), manufacturers choose corrosion-resistant materials and advanced processes. Protective coatings and precision assembly methods are implemented to maximize sensor durability.
6. Testing and Performance Verification in Harsh Conditions
6.1 Accelerated Laboratory Testing
Sensors are subjected to saltwater, chlorine water, and even diiodomethane exposure in controlled environments to monitor signal drift. The results indicate that with targeted design, the sensors exhibit only minor drifts—effects that can be largely attributed to ambient humidity rather than chemical degradation.
6.2 Field Validation
Beyond lab tests, real-world experiments are essential. Extended field trials under actual operating conditions confirm that these sensors consistently provide accurate and stable data, reinforcing confidence in their long-term application.
결론
A thorough review of the sensor’s internal design, 운영 원리, protective packaging, and rigorous testing demonstrates that modern MEMS pressure and temperature sensors deliver both precision and durability, even in corrosive environments. This robust approach underpins the reliability of systems across various sectors, ensuring devices perform consistently over time.
위의 소개는 압력 센서 기술의 적용 표면 만 긁는 것만. 다양한 제품에 사용되는 다양한 유형의 센서 요소를 계속 탐색 할 것입니다., 그들이 어떻게 일하는지, 그리고 그들의 장점과 단점. 여기에서 논의 된 내용에 대한 자세한 내용을 원한다면, 이 안내서의 뒷부분에서 관련 콘텐츠를 확인할 수 있습니다.. 시간이 걸리면, 이 가이드의 세부 사항을 다운로드하려면 여기를 클릭하십시오. 공기 압력 센서 제품 PDF 데이터.
다른 센서 기술에 대한 자세한 내용, 제발 센서 페이지를 방문하십시오.