Կատալոգ
High-precision MEMS negative pressure sensors convert minute diaphragm deflections into electrical signals via capacitive or strain-gauge detection, achieving resolutions down to 10 Pa and nonlinearity below 0.01 % FS in a 0–50 kPa range. Silicon–glass anodic bonding and stress-relief structures ensure hermeticity and minimize thermal stress, yielding stability within ±20 ppm/°C and response bandwidths exceeding 100 kHz. This article presents operating principles, structural design, key performance metrics, installation and welding best practices, pre-production testing tools and methods, and application scenarios—equipping engineers and customers with a reliable, high-value solution for precise negative-pressure data acquisition.
Operating Principle and Structure
Diaphragm & Microcavity Mechanics
A thin silicon or metal diaphragm spans a sealed microcavity; when internal pressure falls below external reference, the diaphragm flexes inward, with displacement roughly linear to negative pressure. Deep reactive ion etching (DRIE) and photolithography define cavity dimensions with submicron precision, ensuring full-scale linearity without residual plastic deformation.
Capacitive vs. Strain-Gauge Detection
In capacitive designs, diaphragm motion changes electrode spacing and thus capacitance, which a precision bridge converts to a voltage signal. Strain-gauge types pattern metallic foil resistors on the diaphragm; bending alters resistance, measured via a Wheatstone bridge for high sensitivity and noise immunity.
Packaging & Stress Isolation
Hermetic sealing employs silicon–glass anodic bonding or low-temperature ceramic bonding to balance vacuum integrity and manufacturability. Internal support pillars or flexible adhesives decouple PCB flexure and thermal expansion stresses from the diaphragm, preserving measurement fidelity.
Thermal Stability & Bandwidth
The diaphragm’s low mass yields intrinsic bandwidths beyond 100 kHz, capturing rapid pressure transients in microsecond timescales. On-chip temperature sensors feed digital compensation algorithms that constrain zero-point and sensitivity drift to below ±20 ppm/°C.
Key Performance Metrics & Characteristics
Ճշգրտություն & Բանաձեվ
Top-tier MEMS negative-pressure sensors achieve overall accuracy of ±0.1 % FS and minimum resolution of 0.01 % Fs, enabling detection of sub-0.01 kPa pressure changes.
Linearity & Hysteresis
Optimized diaphragm geometry and readout circuitry limit linearity error to ≤±0.05 % FS and hysteresis to ≤±0.02 % Fs, ensuring consistent readings during increasing and decreasing pressure cycles.
Temperature Drift & Long-Term Stability
Silicon–glass packaging and stress-buffering structures reduce thermal stress; combined with digital temperature compensation, zero-point and sensitivity drift stay within ±20 ppm/°C, մի քանազոր 5 000 h of accelerated aging tests show <±0.1 % FS drift.
Response Speed & Overload Protection
With response times <10 µs and bandwidths >100 kHz, these sensors excel in fast-transient applications such as medical ventilation. Mechanical stops or diaphragm hard stops typically protect against overpressure up to 200 % Fs.
Power Consumption & Interfaces
Operating currents under 10 մա (power <30 mW) and flexible outputs—analog (0.5–4.5 V), I²C, SPI—permit easy integration with MCUs, PLCs, or DCS for closed-loop control.

Installation & Welding Considerations
Environmental Preparation & Protection
Install sensors away from heavy vibration and corrosive atmospheres; maintain ambient temperatures between –40 °C and 85 °C. Replaceable filters keep particulate and moisture out while allowing airflow.
Low-Heat Welding Methods
Use infrared reflow or laser welding to concentrate heat locally and minimize exposure time. Select no-clean, halogen-free solder pastes to reduce corrosive residues that can degrade sensor packaging.
PCB Layout & Stress Isolation
Limit PCB and component heights to reduce board flexure; include soft mounting pads or flexible supports under the sensor to absorb mechanical and thermal stresses.
ESD Precautions & Cleaning
Handle sensors with grounded ESD protection. Pre- and post-solder cleaning with isopropyl alcohol removes flux residues and prevents long-term contamination.
Pre-Production Testing & Measurement
Calibration Lab Setup
Employ high-precision gas modules (adjustable to ±0.01 Pa) with vacuum and pressure pumps in a closed-loop bench to establish stable reference pressures.
Multi-Point Calibration & Traceability
Use NIST-traceable dead-weight testers or precision manometers to perform at least five-point calibration (zero, full-scale, and intermediate points), logging zero-point, զգայունություն, linearity, and hysteresis data for each sensor.
Automated Data Acquisition & SPC
Integrate 24-bit ADCs with LabVIEW or Python scripts to capture pressure-output curves in real time. Apply Statistical Process Control (SPC) to monitor batch performance, control Cpk, and maintain yields ≥98 %.
Environmental & Aging Tests
Subject sensors to thermal cycling (–40 °C to 85 °C) and humidity stress tests (THB) to evaluate drift, then conduct Highly Accelerated Life Testing (HALT) to uncover latent failure modes and refine design.
Application Scenarios & Customer Value
Medical Ventilation & Suction
Accurate negative-pressure sensing in ventilators and suction devices prevents over-suction injuries and ensures patient safety via automatic pressure regulation.
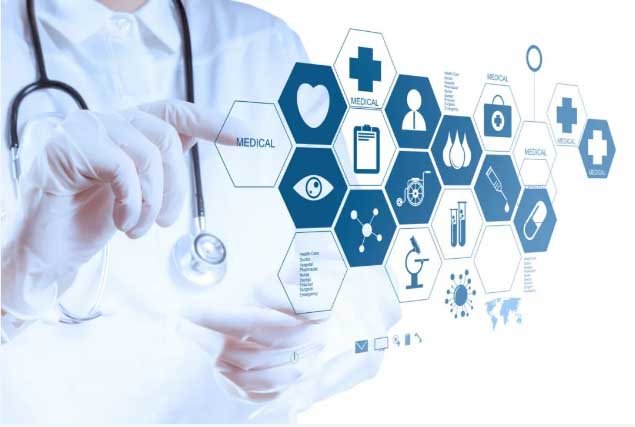
Hvac & Negative-Pressure Isolation
Monitoring room pressure in healthcare facilities, labs, and cleanrooms prevents cross-contamination and optimizes energy efficiency by balancing intake and exhaust flows.
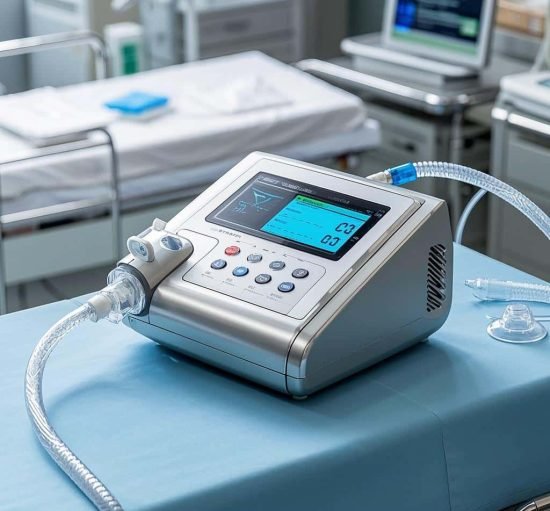
Industrial Vacuum & Microfluidics
In vacuum packaging, semiconductor processing, and lab-on-a-chip systems, precise negative pressure control ensures uniform coating, packaging integrity, and reproducible microfluidic flows.

Research & Emerging Technologies
High-resolution negative pressure data support innovations in micro-nasal flow studies, biochip development, and aerodynamic testing, accelerating lab discoveries toward commercialization.
Եզրափակում
By dissecting the principles, structure, performance, installation practices, pre-production testing, and diverse applications of high-precision MEMS negative pressure sensors, this guide delivers a customer-centric roadmap for implementing reliable, accurate, and robust negative pressure measurement solutions.
Վերոնշյալ ներդրումը միայն քերծում է ճնշման ցուցիչ տեխնոլոգիայի դիմումների մակերեսը. Մենք կշարունակենք ուսումնասիրել տարբեր ապրանքատեսակներում օգտագործվող սենսորային տարրերի տարբեր տեսակները, Ինչպես են նրանք աշխատում, եւ դրանց առավելություններն ու թերությունները. Եթե ցանկանում եք ավելի մանրամասն տեղեկություններ ունենալ, թե ինչ է քննարկվում այստեղ, Այս ուղեցույցում ավելի ուշ կարող եք ստուգել հարակից բովանդակությունը. Եթե ժամանակի համար ճնշված եք, Կարող եք նաեւ սեղմել այստեղ, այս ուղեցույցների մանրամասները ներբեռնելու համար Օդային ճնշման ցուցիչի արտադրանք PDF տվյալներ.
Լրացուցիչ տեղեկությունների համար `սենսորային այլ տեխնոլոգիաների վերաբերյալ, խնդրում եմ Այցելեք մեր տվիչների էջը.