Catalog
As smart manufacturing and high-precision machining demands rise, digital laser sensors play a key role in laser cutting, marking, and inspection equipment. Focusing on the WF5803F series high-precision digital laser sensor, this article breaks down its core technical advantages, system integration and soldering considerations, pre-production testing workflows, and real-time data processing methods. Presented in a concise and customer-centric style, it showcases practical experience and authoritative reliability, offering actionable solutions for laser equipment developers
Technical Background and Value
Evolution of Sensing Requirements in Precision Machining
Modern laser equipment used for micrometer-scale slot cutting, high-speed marking, and nanometer-level inspection requires real-time, high-precision feedback on focus distance, beam intensity, and workpiece position. Traditional analog sensors are prone to environmental interference and lack robustness, making them unsuitable for high-speed dynamic control.
Advantages of Digital Laser Sensing
Digital laser sensors integrate high-resolution ADCs and microprocessors, converting analog optical signals into I²C/SPI digital data. They offer strong noise immunity, stable interfaces, and straightforward communication with host PCs or embedded controllers, enhancing system reliability and maintainability.
Typical Industry Use Cases
In semiconductor wafer cutting, medical device laser welding, and high-end optical fiber alignment, micrometer- to nanometer-level measurement accuracy is critical for yield and quality. Digital laser sensors, with their precision and digital communication, have become standard components in precision equipment.
Core Features and Innovative Advantages of WF5803F
High Resolution and Wide Dynamic Range
The WF5803F delivers 0.01%FS accuracy over a 20 BAR range, with focus distance measurement resolution up to 0.1 μm. It supports real-time, high-frequency data output to meet high-speed dynamic control requirements.
Ultra-Low Latency and High Stability
Internal FPGA-level sampling and calibration algorithms reduce signal processing latency to under 2 ms. Its thermal and vibration immunity ensures stable output under extreme conditions, with fluctuations below ±0.02%.
Multiple Digital Interfaces and Scalability
It supports I²C, SPI, and UART digital interfaces, allowing flexible integration into various laser control boards. The built-in FIFO buffer stores 256 samples, enabling low-frequency reads and reducing bus load.
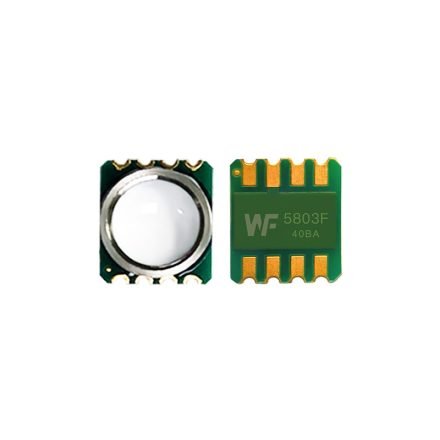
System Integration and Sensor Mounting Considerations
PCB Footprint and Layout
The WF5803F comes in a 4×4 mm LGA package with an optical window on top. In PCB layout, leave an opening above the window, avoid solder mask in that area, and ensure pads are properly metalized for grounding and heat dissipation.
Soldering Process and Temperature Profile
Use a lead-free reflow profile: ramp-up ≤2℃/s, peak at 245±5℃, dwell above 217℃ for 60 s. For rework, use a 350℃ soldering iron for under 3 s to avoid cracking the window glass.
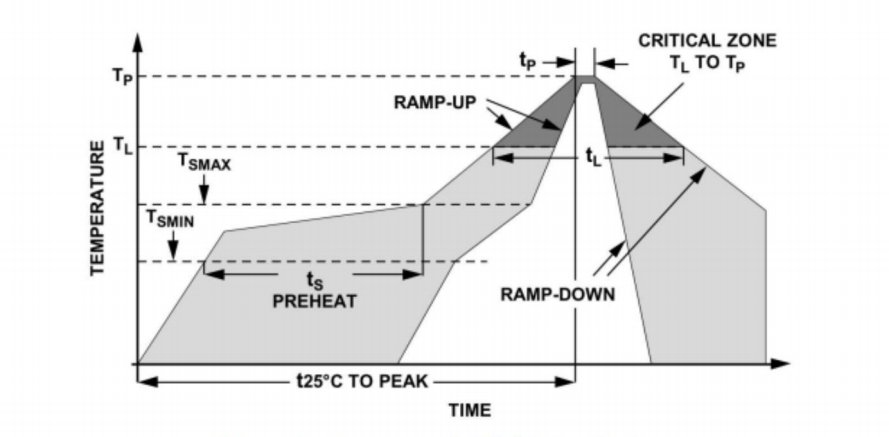
Optical Alignment and Dust Protection
Keep the optical window clean during assembly, avoiding solder paste or flux contamination. After soldering, purge with nitrogen or wipe with a lint-free cloth, and adjust the mounting bracket to ensure the laser beam strikes the center of the window perpendicularly.
Mass-Production Testing Processes and Tools
Overview of Testing Workflow
- Single Unit Verification: Apply known optical or pressure signals on a calibration rig, read digital output, and compare to nominal values.
- Environmental Testing: Run –20 to 80℃ cycles in a thermal-humidity chamber, record temperature drift and compensation coefficients.
- Värähtely & Shock: Conduct 3-axis random vibration tests on a shaker table for vibration immunity; use an impact tester to simulate handling shocks.
Recommended Test Equipment
Precision Calibration Rig: For standard laser power or pressure outputs (esim. Newport spectrometer, Fluke pressure calibrator).
Environmental Chamber: Programmable temperature-humidity cycling.
Vibration/Shock Table: IEC60068 compliant.
Digital Oscilloscope & Logic Analyzer: Monitor I²C/SPI timing and electrical characteristics.
Real-Time Data Processing and Accuracy Optimization
Filtering Algorithms and Sampling Strategy
Use moving average or exponential smoothing filters combined with dynamic sampling: increase to 1 kHz during high-speed cutting, drop to 100 Hz for static inspection to balance responsiveness and noise suppression.
Temperature and Drift Compensation
An onboard temperature sensor provides real-time readings. A second-order polynomial model calculates compensation coefficients on-the-fly. No external calibration points are needed to achieve ±0.01%FS stability across the full temperature range.
Calibration and Self-Diagnostics
At power-up, the device performs a self-test by reading built-in calibration parameters and comparing them to reference curves. If deviations exceed limits, it outputs an error code and switches to a safe mode to ensure process safety.
Johtopäätös
Digital laser sensors deliver core advantages in measurement accuracy, response speed, and system reliability for precision equipment. Taking the WF5803F as an example, its high resolution, low latency, multiple interfaces, and robust environmental immunity strongly support laser cutting, marking, and inspection systems. With proper PCB layout, precise soldering processes, complete mass-production testing, plus real-time filtering and temperature compensation algorithms, equipment developers can rapidly implement efficient, stable sensing solutions and boost product competitiveness.
The above introduction only scratches the surface of the applications of pressure sensor technology. We will continue to explore the different types of sensor elements used in various products, how they work, and their advantages and disadvantages. If you’d like more detail on what’s discussed here, you can check out the related content later in this guide. If you are pressed for time, you can also click here to download the details of this guides air pressure sensor product PDF data.
For more information on other sensor technologies, please visit our sensors page.