With the continuous development of technology, the application of pressure sensors in industries, Cuidado de la salud, automóviles, and consumer electronics is becoming increasingly widespread. Sin embargo, due to the presence of various interference sources such as temperature changes, mechanical vibrations, interferencia electromagnética, etc., the stability and accuracy of sensor performance have become one of the key issues that need to be addressed when designing and manufacturing pressure sensors. This article will explore the anti-interference measures of pressure sensors and provide a detailed introduction from different aspects on how to improve the anti-interference ability of sensors to ensure their reliability and accuracy.
1. Anti interference measures in sensor design
In the design phase of sensors, a series of measures can be taken to enhance their anti-interference ability:
A. Choose the appropriate sensor type: Different applications require different types of pressure sensors, such as resistive, capacitive, and microelectromechanical systems (Mems). Choosing the appropriate sensor type can reduce the risk of environmental interference.
B. Installation of mechanical protection measures: Appropriate mechanical protection can reduce the impact of mechanical vibration, impact, and external forces on sensors. This can be achieved through mechanical design, such as using anti vibration brackets or suspension devices.
C. Optimizing sensor structure: By optimizing the sensor structure, such as reducing internal noise, improving sealing performance, and reducing mechanical distortion, its anti-interference ability can be improved.
2. Temperature anti-interference measures
Temperature changes are a common source of interference that can lead to unstable sensor performance. The following are several anti-interference measures:
A. Temperature compensation: By adding a temperature sensor and using a temperature compensation algorithm, errors caused by temperature can be corrected. This ensures the accuracy of the sensor at different temperatures.
B. Use stable materials: Choose materials with high stability to reduce the impact of temperature on the sensor. Por ejemplo, using materials with low temperature coefficients to manufacture critical components.
C. Thermal isolation: Isolate the sensor from the external environment to reduce the impact of temperature fluctuations. This can be achieved by using insulation materials or cooling systems.
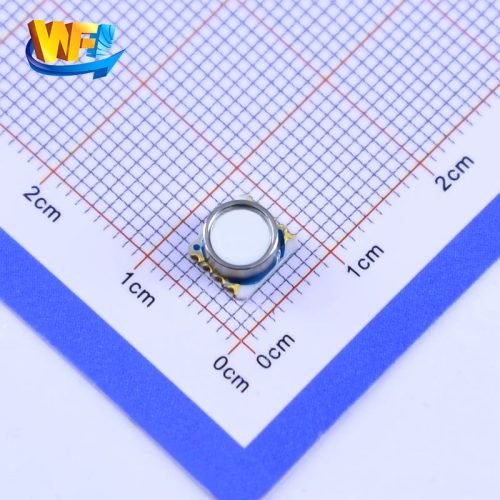
3. Electromagnetic anti-interference measures
Electromagnetic interference is another common issue, especially in industrial environments. Here are some anti-interference measures:
A. Shielding and filtering: Use shielding and filtering in sensor circuits to prevent external electromagnetic noise interference. This can reduce the noise level of the sensor.
B. Grounding and Grounding Isolation: Good grounding design and electrical isolation can reduce the impact of electromagnetic interference. By using differential signal transmission and isolation transformers, common mode interference can be effectively reduced.
4. Data processing and calibration
Data processing and calibration are important steps in improving sensor anti-interference performance:
A. Digital filtering: By using digital filtering algorithms, high-frequency noise and interference signals can be filtered out, improving the accuracy of measurement data.
B. Calibración: Regularly calibrate sensors to correct drift and errors. Calibration can be performed under laboratory conditions or online to adjust sensor output in real-time.
5. Environmental monitoring and feedback control
Finalmente, real-time environmental monitoring and feedback control are also key measures for anti-interference:
A. Monitoreo ambiental: Regularly monitor the temperature, humedad, vibración, and other parameters of the environment in which the sensor is located. This can help identify potential sources of interference and take corresponding measures to address them.
B. Feedback control: Based on environmental monitoring data, take feedback control measures to maintain sensor performance. Por ejemplo, automatically adjusting the working conditions of sensors to adapt to environmental changes.
En general, En aplicaciones prácticas, the anti-interference measures for pressure sensors need to be selected and implemented according to specific circumstances. Taking into account mechanical, electromagnetic, and temperature interference, adopting appropriate designs, materials, and algorithms can effectively improve the performance and reliability of sensors, ensuring accurate pressure measurement data. The successful implementation of anti-interference measures is crucial for pressure sensor applications in various fields, whether used in industrial automation, equipo médico, or automotive safety systems. Only through comprehensive anti-interference strategies can sensors operate stably in harsh environments and meet various application requirements.
Conclusión
The above is the relevant introduction about the anti-interference measures for pressure sensors. That’s all for now. If you want to learn more about the applications of sensors and wireless radio frequency, as well as the introduction of selection knowledge, you can bookmark this website or click on online consultation for a detailed understanding. Además, Weifengheng editor will bring you more industry information about sensors and wireless radio frequency.