Catalogar
En cirugía mínimamente invasiva, El control y el monitoreo de presión del insuflador son fundamentales para la seguridad del paciente y la visualización operativa óptima. Seleccionar el sensor de presión apropiado implica equilibrar la medición de alta precisión, respuesta dinámica rápida, y estabilidad duradera. Este artículo proporciona un análisis completo de los materiales del sensor barométrico MEMS, métodos de embalaje, y procesos de fabricación, cubriendo los requisitos funcionales, parámetros críticos, Las mejores prácticas de instalación y soldadura, Flujos de trabajo de prueba de preproducción, y estrategias de validación de seguridad y confiabilidad. Dirigido a ingenieros y compradores técnicos, Ofrece un enfoque sistemático para determinar la solución ideal del sensor de presión analógica WF100E en rigurosos entornos clínicos y reguladores, Asegurar la integridad del rendimiento del dispositivo incluso después de un uso y esterilización extensos.
Requisitos de rendimiento detallados
1.1 Estándares de precisión y linealidad
Los insuflas requieren sensores con precisión mejor que ± 0.5%FS para controlar estrechamente la discrepancia entre las presiones intraabdominales exhibidas y reales. La alta linealidad garantiza una respuesta proporcional en todo el rango de medición, Reducir la complejidad de la calibración y mejorar la confiabilidad del sistema.
1.2 Sensibilidad y capacidad de respuesta dinámica
Cambios de presión rápida causados por la manipulación del tejido o las oclusiones de tubos demandan la respuesta a nivel de milisegundo y la resolución de alta presión. Microestructuras MEMS, a través de dimensiones de diafragma minimizadas y microcanales optimizados, lograr una detección rápida de variaciones de presión sutiles, salvaguardar el procedimiento quirúrgico.
1.3 Estabilidad a largo plazo y durabilidad
Ciclos de presión repetidos y longevidad del sensor de desafío de esterilización. Los sensores de MEMS premium que utilizan cerámica de silicio o de baja expansión combinadas con sellado de láser o láser mantienen cero deriva por debajo de ± 0.1%FS con el tiempo, Garantizar la consistencia del rendimiento en todo el ciclo de vida del dispositivo médico.
1.4 Comparación de técnicas de materiales y envases
- Opciones de diafragma: Silicon ofrece sensibilidad ultra alta, mientras que el acero inoxidable se destaca en robustez mecánica.
- Métodos de sellado: Los sustratos de cerámica con soldadura por láser ofrecen resistencia a la corrosión superior; Las carcasas metálicas soldadas proporcionan la máxima protección estructural y el blindaje de EMI.
- Prevención de fugas: Junta tórica compuesta y conjuntos de juntas de metal bloquean la entrada de fluidos y agentes de esterilización.
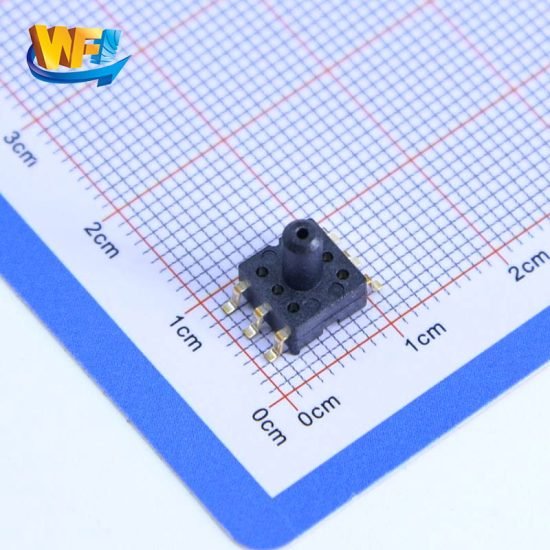
Parámetros de selección crítica explicados
2.1 Margen de coincidencia de rango y seguridad
Con presiones clínicas hasta 20 kPa, Seleccione un rango de sensor de aproximadamente 25 KPA para incluir al menos 20% margen de seguridad, prevenir la sobrecarga de elementos y la preservación de la linealidad a gran escala.
2.2 Resolución e incremento mínimo detectable
Resolución de 0.1 KPA o mejor es necesario para ajustes de presión fina, Alimentar datos detallados para controlar algoritmos para insuflación precisa.
2.3 Compensación de temperatura y tolerancia ambiental
Los circuitos de compensación incorporados limitan la deriva térmica a ± 0.01%FS/℃ entre 20 ℃ –40 ℃, Mantener la estabilidad contra las variaciones ambientales que se encuentran comúnmente en los quirófanos.
2.4 EMC y estándares de resistencia a la interferencia
Las configuraciones médicas están plagadas de fuentes de ruido electromagnéticas; Los sensores deben incorporar el blindaje de EMI, filtrado de entrada, y salidas diferenciales, junto con las prácticas de conexión a tierra y diseño de PCB para garantizar un ruido bajo, Medidas repetibles.
Las mejores prácticas de instalación y soldadura
3.1 Configuración óptima de colocación y tubo
Monte el sensor cerca de la entrada de gas para minimizar las distorsiones inducidas por el tubo. Asegure las curvas graduales y evite los ángulos agudos para evitar la turbulencia de flujo y las lecturas erróneas.
3.2 Temperaturas de soldadura controladas y exposición a la humedad
Use aleaciones de soldadura a baja temperatura (punto de fusión ≤ 250 ℃) y técnicas de reflujo de paso para evitar la degradación de adhesivo interno. Controlar la humedad durante la soldadura para evitar la absorción de humedad por componentes sensibles.
3.3 Estrategias de protección contra el estrés de plomo
Realizar pruebas de tracción posteriores a la soldadura en clientes potenciales, Luego, refuerza las articulaciones con compuestos de silicona o epoxi para distribuir tensiones mecánicas y evitar fallas de fatiga durante el transporte y uso.
3.4 Procedimientos de sellado eléctrico y blindaje
Aplicar recubrimientos conformes a las conexiones eléctricas, Integrar escudos conectados a tierra, y realizar la maceta final para aislar completamente los circuitos internos de entornos externos, elevar el índice de protección a IP67 o superior.
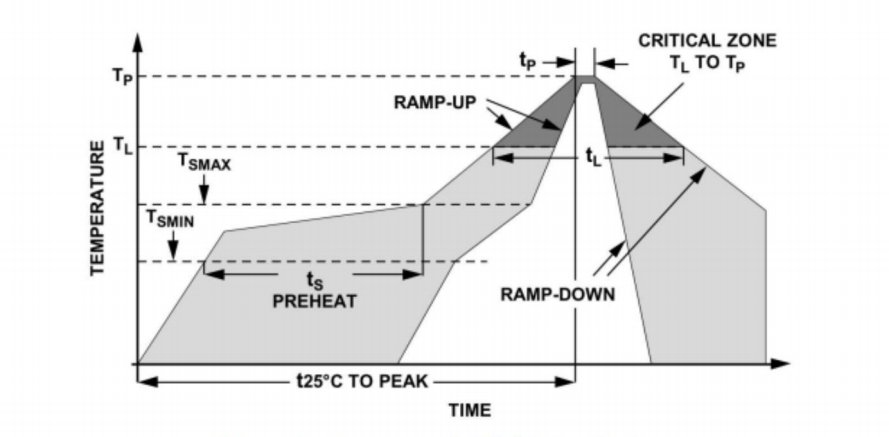
Protocolos de prueba de preproducción y herramientas
4.1 Equipo de calibración y referencia de múltiples puntos
Disgima plataformas de calibración de presión automatizada o probadores de peso muerto para cero, a media escala, y calibración a gran escala. Generar conjuntos de datos de calibración estadística para verificar la consistencia del lote y la distribución de precisión.
4.2 Profiles característicos de salida y métricas de error
Utilice sistemas DAQ de precisión y plantillas personalizadas para realizar barridos de presión, capturar la histéresis y la repetibilidad. Calcular métricas como la no linealidad, histéresis, y repetir precisión para confirmar el rendimiento dentro de los límites de FS de ± 0.5%.
4.3 Envejecimiento ambiental y pruebas de vida aceleradas
Unidades sujetas a 85 ℃/85� ciclos HR y perfiles de vibración para simular el uso a largo plazo. Medir la deriva en desplazamiento cero y sensibilidad después del envejecimiento para modelar el rendimiento de la vida útil del mundo real.
4.4 Instrumentos de laboratorio esenciales e integración de automatización
Equipar instalaciones con multímetros digitales de alta resolución, Circuitos de puente de piedra de trigo, cámaras climáticas, y plataformas de prueba controladas por PLC/PC. Implementar software para la adquisición de datos en tiempo real, análisis, y clasificación automatizada de pases/fallas.
Validación integral de seguridad y confiabilidad
5.1 Diseño de detección redundante y a prueba de fallas
Integre sensores duales o múltiples con la lógica de votación para la redundancia de datos; sobre la falla del sensor primario, cambiar a canales de copia de seguridad y emitir alertas, Mantener un monitoreo de presión ininterrumpido.
5.2 Análisis de ciclismo y fatiga a largo plazo
Ejecutar miles de ciclos de presión en condiciones clínicas simuladas, Monitoreo de parámetros Drift y desviaciones inducidas por fatiga para informar los horarios de mantenimiento e intervalos de servicio.
5.3 Tolerancia a la sobrecarga y pruebas de choque
Realice pruebas de sobrecarga estática a 1.5–2 × FS y un shock múltiple por IEC 60068-2-27 para verificar la resiliencia del diafragma y la integridad del paquete bajo cargas extremas.
5.4 Cumplimiento regulatorio y certificación médica
Adherirse a ISO 13485 Requisitos de gestión de calidad y compilar verificación de diseño, Evaluación de riesgos, y documentos de biocompatibilidad para el marcado CE y la autorización de la FDA, Garantizar la alineación regulatoria completa.
Conclusión
Esta guía ofrece una metodología exhaustiva para seleccionar el sensor de presión de MEMS analógicos WF100E para insufladores médicos, cubriendo opciones de material avanzado, Métricas de rendimiento de precisión, Instalación refinada y procesos de soldadura, Pruebas de preproducción rigurosas, y estricta validación de seguridad. El empleo de estas mejores prácticas garantiza que los insufladores entreguen precisos, confiable, y control de presión seguro, En última instancia, apoyando cirugías mínimamente invasivas exitosas y bienestar del paciente.
La introducción anterior solo rasca la superficie de las aplicaciones de la tecnología del sensor de presión. Continuaremos explorando los diferentes tipos de elementos de sensores utilizados en varios productos., Cómo funcionan, y sus ventajas y desventajas. Si desea más detalles sobre lo que se discute aquí, Puede consultar el contenido relacionado más adelante en esta guía. Si está presionado por el tiempo, También puede hacer clic aquí para descargar los detalles de estas guías Producto del sensor de presión de aire datos PDF.
Para obtener más información sobre otras tecnologías de sensores, por favor Visite nuestra página de sensores.
Aprecio cómo este blog desglose las diferencias entre los sensores estándar y de grado de precisión..