Katalog
In smart coffee machines, high-precision pressure sensors are the core components that ensure robust extraction, stable flow rates, and consistent flavor. The WF5803C 0–30 bar absolute-pressure MEMS sensor module integrates a piezoresistive silicon element with a 16-bit ADC and stores six on-chip calibration coefficients for software compensation, significantly enhancing measurement accuracy and consistency. Its ceramic substrate, antimagnetic stainless-steel sealing ring, and O-ring design guarantee high-pressure tolerance (up to 5× rated range) and corrosion resistance, while low-voltage automatic power-down capability and low power consumption support long-term reliable operation. A 3-wire serial interface plus a 32.768 kHz clock line simplifies microcontroller integration. This article examines the WF5803C’s application requirements, device selection and cost considerations, recommendations for replacing legacy pressure sensors, Installation und Löten Best Practices, pre-production testing workflows, and measurement tools—guiding engineers and procurement managers toward a robust, scalable smart coffee-machine pressure-monitoring solution.
Application Requirements and Functional Considerations
1.1 Precision and Response for Stable Extraction
In smart espresso machines, extraction pressure directly impacts crema quality and taste consistency. While 9 bar is the market standard, high-end machines often require a 0–30 bar absolute range to cover pre-infusion, brewing, and cleaning phases. The WF5803C’s 0–30 bar range with its 16-bit ADC delivers ±0.1 %FS accuracy and millisecond-level response, meeting the dynamic pressure-control needs of premium all-in-one machines.
1.2 On-Chip Calibration and Temperature Compensation
Temperature drift is a major source of long-term accuracy degradation. WF5803C stores six calibration coefficients on-chip, enabling software linearization and thermal compensation that keeps errors within ±0.2 %FS from 0 °C to 85 ° C. Systems can periodically reapply these coefficients in-field to further minimize batch-to-batch variation.
1.3 Durability and Reliability
Smart coffee machines must endure repeated high-pressure cycles. The WF5803C uses an antimagnetic polished stainless-steel ring and O-ring seal to withstand pressures up to five times its rated range without leakage or failure. Its ceramic substrate and automatic power-down feature extend both electrical and mechanical life.
1.4 Cost Analysis and Legacy Replacement
Compared to mechanical gauges, MEMS modules like the WF5803C can be mass-produced at roughly US $3–6 per unit (depending on volume), offering a smaller footprint, no moving parts, and zero magnetic hysteresis. For machines currently using mechanical or analog strain-gauge schemes, the WF5803C provides a seamless digital upgrade—shortening calibration time on the production line and reducing maintenance costs.
1.5 Interface and System Integration
The WF5803C communicates over a 3-wire serial bus (clock/data/chip-select) plus a 32.768 kHz reference clock line, simplifying PCB routing and supporting low-speed SPI or custom MCU protocols. Its 1.8–3.3 V operating range and µA-level standby consumption make it easy to integrate with modern microcontrollers and SoC platforms.
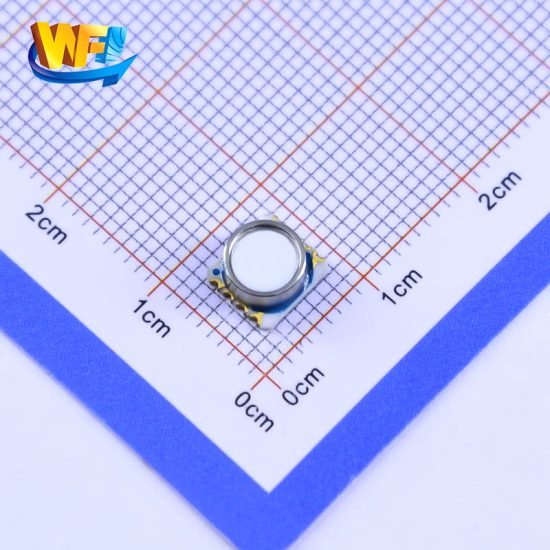
Installation & Soldering Guidelines
2.1 Pre-installation & Machine State
Always mount the sensor on a cold, pressure-free system. Any residual pressure or heat can deform the O-ring during threading, causing micro-leaks and unstable readings. After shutdown, allow at least 15 minutes for lines to cool and fully depressurize.
2.2 Sensor-Body Interface Matching
Because the WF5803C uses an antimagnetic stainless-steel ring and O-ring seal, use a fitting made from the same stainless-steel grade (304 or 316L) to avoid stress from differing thermal-expansion coefficients. Apply only PTFE tape—no silicone or oil-based thread lubricants—to prevent chemical attack or diaphragm contamination.
2.3 Soldering Profile & Temperature Control
Although the module itself is not subject to high-temperature wave reflow, its LGA-8 ceramic pads are heat-sensitive. Use a five-step reflow profile with a peak of ≤ 240 ° C für nicht mehr als 30 seconds to avoid substrate warpage or die stress. For manual soldering, keep the iron tip at ≤ 350 °C and limit contact time to ≤ 3 seconds per pad.
2.4 ESD Protection & Cleaning
Handle components at an ESD-safe workstation, wearing a grounded wrist strap. Avoid touching the diaphragm side; grip edges only. Do not spray alcohol- or water-based cleaners near the sensing area to prevent fluid ingress and output drift.
2.5 Securing & Vibration Damping
To withstand high-pressure rinses and mechanical vibration, install a lock washer or spring washer under the sensor flange. For heavy vibration environments, insert a silicone damping pad between the sensor body and chassis to mitigate long-term mechanical stress.
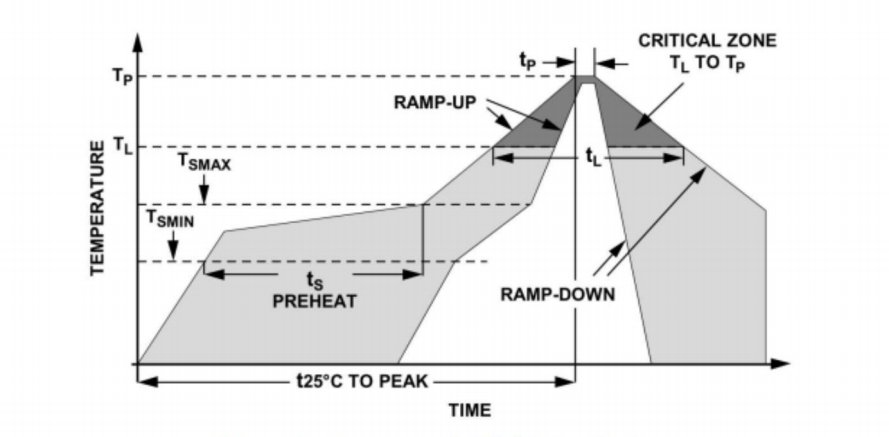
Test & Measurement Tools
Before integrating the WF5803C into a smart coffee machine, validate its performance using professional test and measurement equipment:
Programmable Three-Port Pressure Calibrator:
Generates precise pressures from 0–30 bar and measures voltage/current outputs to verify linearity and full-scale accuracy.
Dynamic Pressure Calibration Workstation:
A handheld system for rapid on-line calibration and re-testing on production lines, ensuring batch consistency.
Tri-Zone Environmental Chamber:
Cycles the sensor between 0 °C and 85 °C to assess thermal-drift performance while capturing raw 16-bit ADC outputs for software compensation verification.
In-System Validation Tool (z.B., Scace 2):
Integrates a pressure gauge and thermocouple at the group head to record dynamic pressure and temperature profiles during real extractions.
Automated MEMS Test Cell:
Provides pick-and-place handling, programmable physical stimuli, and full electrical testing for high-throughput final-test calibration, including thermal and functional tests.
Pre-Production Testing Workflow
Visual & Solder-Joint Inspection:
Use automated optical inspection (AOI) to check for cracks or solder voids on the LGA-8 pads and stainless-steel ring.
Array Pressure Calibration:
Calibrate batches (bis zu 1 000 units) bei 0, 15, Und 30 Bar, logging offset, gain, and linearity errors.
Thermal Drift Verification:
Thema 10 % of units to temperature cycles at 0 ° C, 25 ° C, Und 85 ° C, comparing pre- and post-compensation errors.
Accelerated Damp-Heat Stress:
Age sensors at 85 °C/85 %RH for 72 Std., sampling every 12 hours to filter out drift-out-of-spec units.
In-Machine Spot Check:
Mount sample modules in a test espresso machine and run extraction profiles, verifying dynamic response and steady-state accuracy.
Final QC & Release:
Auto-generate pass/fail reports, integrate test data into the manufacturing execution system (MES), and route failures for rework or scrap.
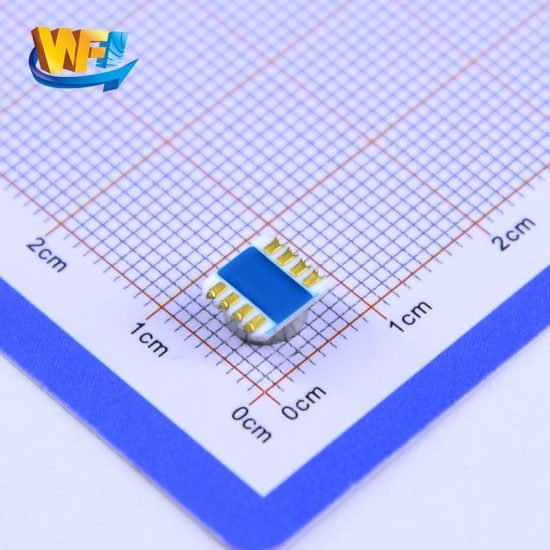
Legacy Sensor Replacement Recommendations
For machines still using strain-gauge or analog voltage-output schemes, upgrading to the WF5803C offers:
Simplified Interface & Leiterplatte: On-board 16-bit ADC and 3-wire serial bus eliminate external amplifiers and filters, reducing board space and EMI susceptibility.
Lower Total Cost: Higher unit cost up front is offset by reduced BOM items and fewer field calibrations, lowering overall production and maintenance costs by 20 %–30 %.
Improved Accuracy & Stabilität: Achieves ±0.1 %FS accuracy with zero magnetic hysteresis, versus ±1 %FS and hysteresis in strain-gauge designs.
Automation Compatibility: Seamlessly integrates with automated MEMS test cells for high-speed calibration and sorting, boosting throughput by 3×–5×.
Robust Environmental Performance: Stainless-steel seal and ceramic substrate support stable operation at 85 °C/85 %RH and in magnetic fields, ideal for commercial and automatic machines.
Abschluss
The WF5803C 0–30 bar absolute-pressure MEMS sensor module combines a 16-bit ADC, six on-chip compensation coefficients, and proven thermal compensation to deliver ±0.1 %FS accuracy, millisecond-scale response, and long-term stability for smart coffee machines. Leveraging professional calibration tools (pressure calibrators, MEMS test cells, in-system validators) and a rigorous pre-production workflow bridges the gap from prototype to high-volume manufacturing. Compared to mechanical or analog solutions, the WF5803C simplifies design and calibration, enhances reliability, and reduces total cost of ownership—empowering coffee-machine makers to achieve rapid digital transformation and scalable production.
Die obige Einführung kratzt nur die Oberfläche der Anwendungen der Drucksensortechnologie. Wir werden weiterhin die verschiedenen Arten von Sensorelementen untersuchen, die in verschiedenen Produkten verwendet werden, wie sie funktionieren, und ihre Vor- und Nachteile. Wenn Sie mehr Details darüber möchten, was hier besprochen wird, Sie können den zugehörigen Inhalt später in diesem Handbuch überprüfen. Wenn Sie auf Zeit gepresst werden, Sie können auch hier klicken, um die Details dieser Leitfäden herunterzuladen PDF -Daten des Luftdrucksensorprodukts.
Weitere Informationen zu anderen Sensortechnologien, Bitte Besuchen Sie unsere Sensors -Seite.