Catalog
MEMS pressure-temperature integrated sensors play a crucial role in modern mechanical equipment, with their reliable performance directly impacting overall system operational stability. Small-scale resistive MEMS sensors like the WF100E provide ideal solutions for engineers through built-in temperature compensation and high-precision measurement capabilities. This article analyzes the performance characteristics of pressure-temperature sensors in mechanical equipment integration applications, focusing on accuracy, response speed, durability, and reliability indicators under harsh operating environments. Through in-depth analysis of sensor core technical parameters, we provide practical reference guidance for technical decision-makers in equipment selection and system design.

Technical Foundation and Integration Advantages of MEMS Pressure-Temperature Sensors
MEMS pressure-temperature sensors represent a significant breakthrough in microelectromechanical systems technology within industrial measurement applications. The WF100E sensor employs resistive measurement principles, integrating piezoresistive effects with temperature sensing functionality on a single chip, achieving space minimization while maximizing measurement accuracy. This integrated design eliminates signal transmission losses and temperature drift issues found in traditional separate sensor systems, providing more stable and reliable monitoring solutions for mechanical equipment.
The core of resistive MEMS technology lies in the piezoresistive characteristics of silicon crystals. When external pressure acts on the sensor diaphragm, the internal crystal resistance values undergo minute but measurable changes. These changes maintain a proportional relationship with applied pressure, enabling high-precision pressure measurement through precision signal conditioning circuits. Simultaneously, the built-in temperature sensor continuously monitors environmental temperature changes, providing real-time temperature compensation data for pressure measurements, ensuring measurement accuracy across wide temperature ranges.
Miniaturization design represents one of the most significant advantages of MEMS sensors. The compact size of the WF100E sensor enables easy integration into space-constrained mechanical equipment, while SMD surface mount technology further simplifies installation processes. This mounting approach not only improves production efficiency but also enhances connection mechanical strength and electrical stability. O-ring seal design ensures long-term reliable operation in humid or corrosive environments, particularly important for outdoor or industrial environment mechanical equipment.
Low power consumption characteristics make MEMS sensors especially suitable for battery-powered or energy-sensitive applications. Advanced circuit design controls static power consumption to microampere levels, while dynamic measurement power consumption remains at milliwatt levels. This low power characteristic extends equipment operational cycles, reduces maintenance frequency, and lowers total ownership costs.
Signal Processing and Digitization Advantages
Modern MEMS pressure-temperature sensors integrate advanced signal processing capabilities, with built-in analog-to-digital converters directly converting analog signals to digital outputs, eliminating external ADC requirements. This integrated design not only simplifies system architecture but also improves signal interference resistance. Digital outputs can directly connect with microcontrollers or industrial bus systems, enabling rapid data acquisition and processing.
High resolution represents another important characteristic of MEMS sensors. Through precision manufacturing processes and advanced signal processing algorithms, modern sensors can achieve 16-bit or even higher resolution, capable of detecting extremely small pressure changes. This high resolution capability enables sensors to monitor minute anomalies during mechanical equipment operation, providing important data support for preventive maintenance.
Performance Requirements and Challenges in Mechanical Equipment Operating Environments
Mechanical equipment operating environments typically possess high complexity and harshness, imposing strict performance requirements on integrated pressure-temperature sensors. Industrial environment factors including temperature fluctuations, vibration impacts, electromagnetic interference, and chemical corrosion all influence sensor performance. Understanding these challenges and selecting appropriate sensor specifications is key to ensuring reliable system operation.
Temperature variation represents one of the primary factors affecting sensor performance. Mechanical equipment generates substantial heat during operation, causing rapid local temperature increases, while temperatures drop quickly during shutdown periods. This temperature cycling affects both material characteristics and electrical performance of sensors. Temperature-compensated sensors like the WF100E utilize built-in temperature sensors to monitor environmental temperatures in real-time, adjusting pressure measurement results according to preset compensation algorithms, effectively eliminating temperature drift effects on measurement accuracy.
Vibration and shock are unavoidable phenomena in mechanical equipment operation. Rotating machinery imbalance, reciprocating motion inertial forces, and sudden mechanical failures all generate intense vibration and shock. Silicon-based MEMS sensor structures possess good vibration resistance, but installation design must still consider vibration isolation and shock absorption measures. Appropriate installation design can significantly improve sensor reliability and service life in harsh vibration environments.
Electromagnetic interference becomes increasingly severe in modern industrial environments. High-power motors, variable frequency drives, switching power supplies, and wireless communication devices all generate intense electromagnetic radiation. Digital output and built-in filtering circuits of MEMS sensors provide good interference resistance, but installation still requires attention to shielding and grounding measures, ensuring signal transmission stability and accuracy.
Pressure Range Adaptability Analysis
Different types of mechanical equipment have varying pressure measurement range requirements. Hydraulic systems typically operate in high-pressure environments, with pressure ranges potentially from several hundred PSI to thousands of PSI. Pneumatic systems operate at relatively lower pressures, typically between tens to hundreds of PSI. MEMS pressure sensors must select appropriate pressure ranges based on specific applications, ensuring both measurement accuracy and adequate overload protection capability.
Overload protection represents an important indicator for evaluating sensor reliability. Quality MEMS pressure sensors typically possess the capability to withstand twice the rated pressure without permanent damage. This overload protection capability provides safety assurance for systems under abnormal operating conditions, preventing sensor damage and system failures due to sudden pressure changes.
Response speed represents another key performance indicator. In rapidly changing pressure environments, sensors must be able to track pressure changes promptly, providing real-time feedback information for control systems. The small mass characteristics of MEMS sensors enable rapid response capability, with typical response times at millisecond levels, meeting dynamic monitoring requirements of most mechanical equipment.
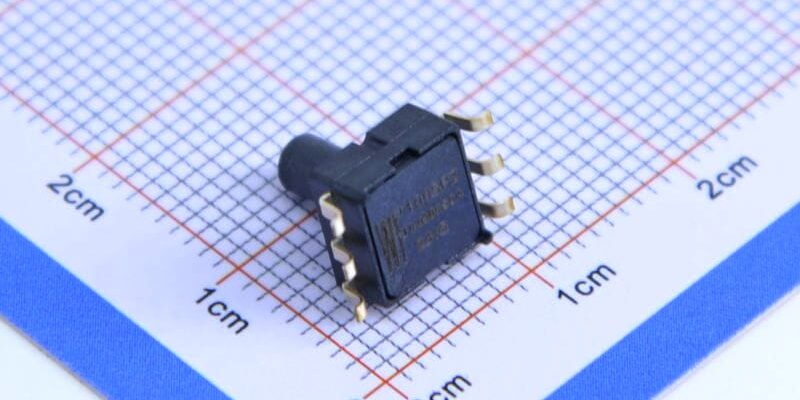
Critical Role of Temperature Compensation Technology in Equipment Reliability
Temperature compensation technology represents the core technology ensuring MEMS pressure sensors maintain high-precision measurement across wide temperature ranges. Mechanical equipment experiences significant temperature changes during operation, from ambient temperature at startup to high-temperature states during stable operation, with temperature change ranges potentially reaching tens or even hundreds of degrees. Without effective temperature compensation, sensor measurement errors would increase significantly with temperature changes, seriously affecting system control accuracy and reliability.
Built-in temperature sensors form the foundation for achieving precise temperature compensation. The WF100E sensor integrates high-precision temperature sensing elements capable of real-time monitoring of sensor chip temperature changes. This design ensures temperature measurement accuracy and real-time capability, providing reliable data foundation for temperature compensation algorithms. Compared to external temperature sensors, built-in design eliminates temperature gradient errors between temperature and pressure sensors, significantly improving compensation accuracy.
Precise calibration of temperature coefficients represents the key component of temperature compensation technology. Each sensor undergoes rigorous temperature cycling tests during manufacturing, measuring output characteristics at different temperatures. Through multi-point temperature calibration, precise temperature compensation models can be established, minimizing temperature effects on pressure measurement. Advanced sensors also employ nonlinear compensation algorithms, further improving measurement accuracy across wide temperature ranges.
Real-time compensation algorithm implementation requires powerful signal processing capabilities. Modern MEMS sensors integrate dedicated digital signal processors capable of real-time execution of complex temperature compensation calculations. This real-time processing capability ensures every measurement undergoes accurate temperature compensation, providing stable and reliable measurement results regardless of environmental temperature changes.
Long-term Stability Assurance Mechanisms
Long-term stability represents an important indicator for evaluating sensor reliability. Mechanical equipment typically requires continuous operation for months or even years, with sensors maintaining stable performance throughout long-term use. Temperature compensation technology not only addresses short-term temperature effects but also maintains long-term stability through periodic self-calibration functions.
Thermal matching design of materials represents a key factor ensuring long-term stability. All sensor components utilize materials with matched thermal expansion coefficients, reducing temperature cycling effects on mechanical structures. Silicon-based MEMS structures possess excellent thermal stability, maintaining stable mechanical and electrical characteristics across wide temperature ranges.
Packaging technology improvements further enhance sensor environmental adaptability. Advanced packaging materials and processes ensure long-term reliable operation in harsh environments. O-ring seal design not only provides excellent protection performance but also maintains superior thermal conduction characteristics, ensuring built-in temperature sensors can accurately sense environmental temperature changes.
Performance Advantages and Adaptability Analysis
MEMS pressure-temperature sensors demonstrate significant performance advantages in mechanical equipment integration applications, making them ideal choices for modern industrial automation systems. High-precision measurement capability represents the most prominent advantage. Through advanced manufacturing processes and precision signal processing technology, modern MEMS sensors can achieve 0.1% or higher measurement accuracy, sufficient to meet the most demanding industrial application requirements.
Low noise characteristics represent another important advantage of MEMS sensors. Resistive measurement principles inherently possess good signal-to-noise ratios, combined with advanced signal conditioning circuits and digital filtering technology, effectively suppressing various noise interference. This low noise characteristic enables sensors to detect minute pressure changes, providing reliable data support for precision control and fault warning. In mechanical equipment preventive maintenance, this capability is particularly important, enabling early detection of potential equipment anomalies.
Rapid response capability enables MEMS sensors to track rapidly changing pressure signals. In dynamic applications such as pulsating pressure monitoring or rapid pressure control, sensor response speed directly affects system performance. MEMS technology’s inherent characteristics determine extremely small inertia, enabling millisecond-level response speeds, meeting monitoring requirements of high-speed mechanical equipment.
High sampling rates represent a significant characteristic of digital MEMS sensors. Through built-in high-speed ADCs, sensors can achieve kilohertz or even higher sampling rates, providing rich data for frequency domain analysis and dynamic characteristic research. This high sampling rate capability enables engineers to deeply analyze mechanical equipment operational characteristics, discovering abnormal phenomena undetectable through traditional low-speed sampling.
Environmental Adaptability Assessment
Environmental adaptability represents a key performance indicator for MEMS sensors in practical applications. Industrial environment complexity requires sensors to possess excellent environmental adaptation capabilities, including temperature adaptability, humidity tolerance, chemical compatibility, and mechanical strength. Advanced sensors like the WF100E achieve wide-range environmental adaptability through carefully designed packaging structures and material selection.
Temperature adaptability represents the most basic and important environmental performance. Industrial-grade MEMS sensors typically operate normally within wide temperature ranges from -40°C to +125°C, with some special application sensors capable of withstanding even more extreme temperature conditions. Built-in temperature compensation functions ensure high-precision measurement across the entire operating temperature range.
Humidity and corrosive environments pose serious challenges to sensor long-term reliability. O-ring seal design provides effective protection, preventing moisture and corrosive gases from entering sensor interiors. Simultaneously, sensor housing materials undergo special treatment, possessing good corrosion resistance, enabling long-term stable operation in harsh chemical environments.
Mechanical strength represents the key to sensor survival in vibration and shock environments. Silicon-based MEMS structure materials possess excellent mechanical characteristics, capable of withstanding intense vibration and shock without structural damage. Reasonable installation design and shock absorption measures further improve sensor reliability in harsh mechanical environments.
Measurement Accuracy Verification and Quality Assessment Tools
Ensuring measurement accuracy and reliability of MEMS pressure-temperature sensors requires professional testing equipment and evaluation methods. Engineers must conduct systematic testing verification when selecting supplier products to confirm sensors can meet specific project requirements. This verification process involves not only basic accuracy testing but also long-term stability evaluation, environmental adaptability testing, and reliability analysis.
Pressure accuracy testing requires high-precision pressure standards as references. Dead weight pressure testers are considered the most accurate pressure standards, achieving accuracies of 0.01% or higher. Through comparative testing with pressure standards, sensor measurement errors at different pressure points can be accurately evaluated. Testing processes must consider environmental factor influences such as temperature and humidity, ensuring test result accuracy and repeatability.
Temperature accuracy verification is equally important, particularly for sensors integrating temperature compensation functions. Precision temperature calibrators and constant temperature chambers are essential equipment for temperature testing. Through testing at different temperature points,
Conclusion
The reliability of pressure and temperature sensors in mechanical equipment integrated applications is directly related to the operational stability and safety of the entire system. Through in-depth analysis of MEMS technology foundation, environmental adaptability, temperature compensation mechanism and performance verification methods, we can see that modern integrated sensors have the technical capabilities to meet the needs of demanding industrial applications.
Advanced MEMS pressure and temperature sensors such as WF100E provide engineers with high-precision and high-reliability measurement solutions through technical features such as resistive measurement principle, built-in temperature compensation, miniaturized design and digital output. Its stable performance over a wide temperature range, excellent environmental adaptability and fast response characteristics make it an ideal choice for modern mechanical equipment monitoring and control systems.
When selecting and applying such sensors, engineers need to comprehensively consider multiple factors such as accuracy requirements, environmental conditions, installation constraints and long-term reliability. Through systematic performance verification and quality evaluation, it can be ensured that the selected sensor can provide stable and reliable services in the expected application environment. With the continuous development and improvement of MEMS technology, integrated sensors will play an increasingly important role in improving the reliability and intelligence level of mechanical equipment.
The above introduction only scratches the surface of the applications of pressure sensor technology. We will continue to explore the different types of sensor elements used in various products, how they work, and their advantages and disadvantages. If you’d like more detail on what’s discussed here, you can check out the related content later in this guide. If you are pressed for time, you can also click here to download the details of this guides air pressure sensor product PDF data.
For more information on other sensor technologies, please visit our sensors page.