Catalog
How to Troubleshoot Common Pressure Sensor Problems
Pressure sensors are an essential component in many industrial and commercial applications, providing real-time pressure measurements that are critical for controlling and monitoring various processes. However, as with any mechanical device, pressure sensors can sometimes fail. In this article, we’ll provide a guide on how to troubleshoot common pressure sensor problems, including how to diagnose and repair WF pressure sensors as well as other sensors.
No output or unstable output
If your pressure transducer has no output or an erratic output, there may be a problem with the transducer’s electrical connections or with the transducer itself. Check the pins to make sure the connections are correct and test the sensor output voltage with a multimeter or air pressure sensor module. If the voltage is within the specified range, the problem may be with the sensor itself. In this case, please contact WFsensors Technical Support for assistance.
Zero Output
If your pressure transducer outputs zero, there may be a problem with the transducer’s electrical connections, the transducer’s supply voltage, or the transducer’s internal electronics. Check the wiring pinout diagram and supply voltage to make sure they are connected correctly and within the specified range. If the pins are soldered and the voltage is correct, the problem may be with the sensor’s internal electronics. In this case, contact factory support for assistance.
Out of Range Output
If your pressure transducer’s measured output is outside of the pressure range, it may be due to excessive pressure, a faulty transducer, or a problem with the calibration of the transducer. Check the pressure to make sure it is within the rated range of the sensor. If the pressure is within the specified range, the problem may be with the sensor or its calibration. In this case, the factory can be contacted for a new air pressure sensor.

Remark:the connections definition is same for SOP and DIP package product
Slow or Delayed Response
If your pressure transducer has a slow or delayed response, it may be due to a problem with the transducer’s electronics, wiring, or calibration. Please check the wiring connections to ensure that they are correct and free of corrosion. Check the calibration of the sensor to make sure it is within specified limits. If the soldered pin connections and calibration are correct, the problem may be with the sensor’s internal electronics.
Temperature Drift
If your pressure transducer is experiencing temperature drift, it may be due to a problem with the transducer’s compensation circuitry or the calibration of the transducer. Check the pin wiring to ensure that the connections are correct and free of corrosion. Check the calibration of the sensor to make sure it is within the specified range. If the wiring and calibration are correct, the problem may be with the sensor’s compensation circuitry.
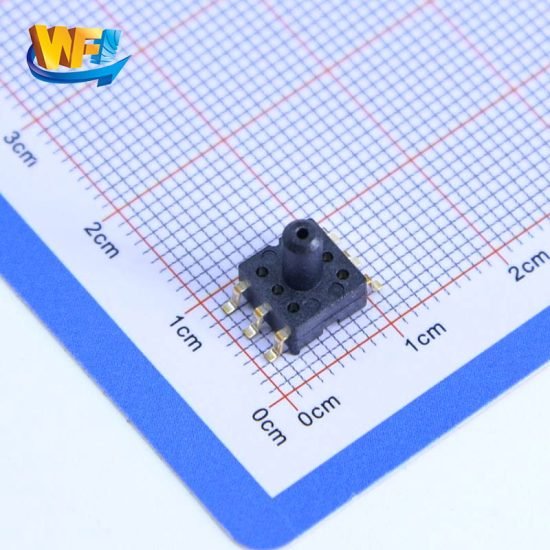
Why do pressure sensors fail?
Environmental Factors
Harsh environments can significantly impact sensor performance. Exposure to extreme temperatures, humidity, corrosive substances, and vibration can accelerate wear and tear. Protecting the sensor with appropriate enclosures and coatings is essential.
Electrical Overstress
Electrical overstress, such as voltage spikes or electrostatic discharge (ESD), can damage the sensor’s internal electronics. Proper grounding, surge protection, and careful handling can prevent these issues.
Contamination
The presence of contaminants, such as dust, oil, or chemicals, can clog the sensor’s pressure port or corrode its internal parts. Regular cleaning and the use of filters can prevent contamination-related failures.
How to Troubleshoot Common Pressure Sensor Problems
Initial Checks
Visual Inspection: Check for any visible damage, such as cracks, corrosion, or loose connections.
Wiring: Ensure all wiring connections are secure and correctly wired according to the sensor’s datasheet.
Power Supply: Verify that the sensor is receiving the correct supply voltage. Often, it’s inadequate voltage.
Pressure Checks
Apply Known Pressure: Use a calibrated pressure source to apply known pressures to the sensor.
Compare Readings: Compare the sensor’s output with the expected values. Any significant deviation indicates a problem.
Check for Leaks: Ensure there are no leaks in the pressure line or fittings that could affect the sensor’s readings.
- Signal Conditioning: Check the signal conditioning circuitry for any issues, such as faulty op-amps or resistors.
Заключэнне
The above introduction only scratches the surface of the applications of pressure sensor technology. We will continue to explore the different types of sensor elements used in various products, how they work, and their advantages and disadvantages. If you’d like more detail on what’s discussed here, you can check out the related content later in this guide. If you are pressed for time, you can also click here to download the details of this guides air pressure sensor product PDF data.
For more information on other sensor technologies, please visit our sensors page.